I have grown up hearing about the banana plant’s versatility and that every part of it is useful. From using the leaves as serving plates to the stem, flower, and fruit, all are edible. The only waste generated from a banana farm is the two outermost layers: the sheaths of the banana stem. Typically, these are either burnt or dumped as garbage.
But PM Murugesan, a resident of Melakkal village in Madurai district, almost two decades ago, found a way to use this residual banana fibre to weave them into ropes. These could then be used to make various products like mats, bags, etc. In this exclusive interview with The Better India, Murugesan, founder of M S Ropes Production Center, speaks about his journey, setting up a company, winning awards and accolades, and having a machine patented by him.
Finding treasure in trash
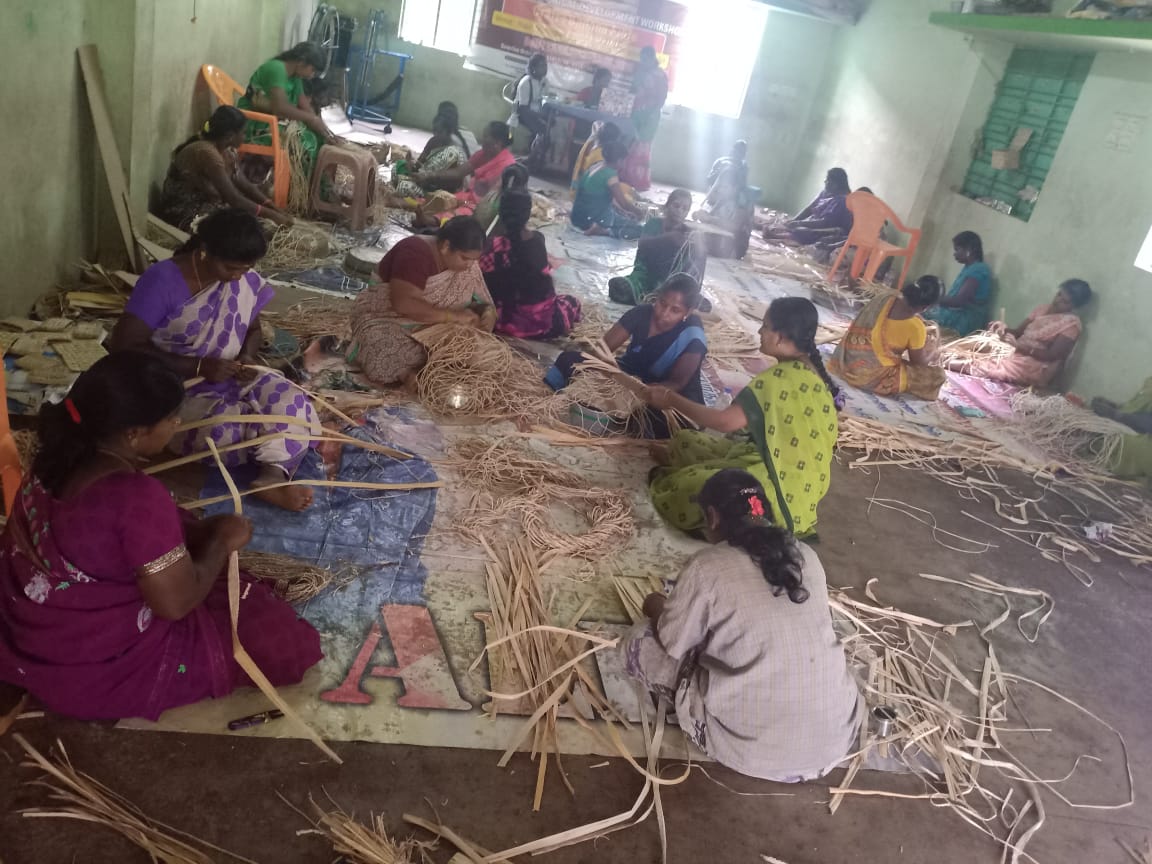
Even though Murugesan could not complete his education beyond class 8 because of his family’s poor financial conditions, his achievements are truly remarkable.
“I had to be pulled out of school and join my father in the fields because we did not have the money for me to continue studying. Mine was a traditional agricultural family and one didn’t necessarily see much use in me continuing to study,” he says. Murugesan grew up encountering many agriculture failures, and he mentions how even the intervention of the State Agricultural Department did not yield any good results.
Though, there was a lot of waste generated from banana farms around him, which made him think of ways to use it.
It was around 2008 when Murugesan, his wife, Malarkodi, and the other family elders started discussing utilising the banana plant waste. “The idea struck me when I saw the banana thread being used to thread flowers for garlands. But it was difficult in the beginning as the rope would not stay connected, and kept splitting,” he says. Early on, no machine could be used for the banana fibre, and Murugesan speaks about how most of the work was done manually or on makeshift machines.
In his native area, Murugesan says some machines are used to process coconut husk into ropes, and he first tried processing the banana fibre also in the same machine. “Unfortunately, that did not work. So I used that as my base and modified it to work well for processing banana fibre,” he says. After its success, he added a motor to it to ensure that the production could be faster.
After a series of trial-and-error, he developed a spinning machine using bicycle wheel rims and pulleys. This was a frugal innovation at its best. “What we do is braid the strands together to achieve a good tensile strength. We had to make sure that the products that we were making out of this were worth the money,” he adds. Wanting to better this process, Murugesan invested close to Rs 1.5 lakhs and built and patented his own machine. “Once the machine was made, I approached the Biotechnology Industry Research Assistance Council (BIRAC) and presented the same there. I also requested for help from the institute, and after they visited and liked my machine, they recommended this machine be used by other farmers in the area as well,” he says.
Building the company, one step at a time
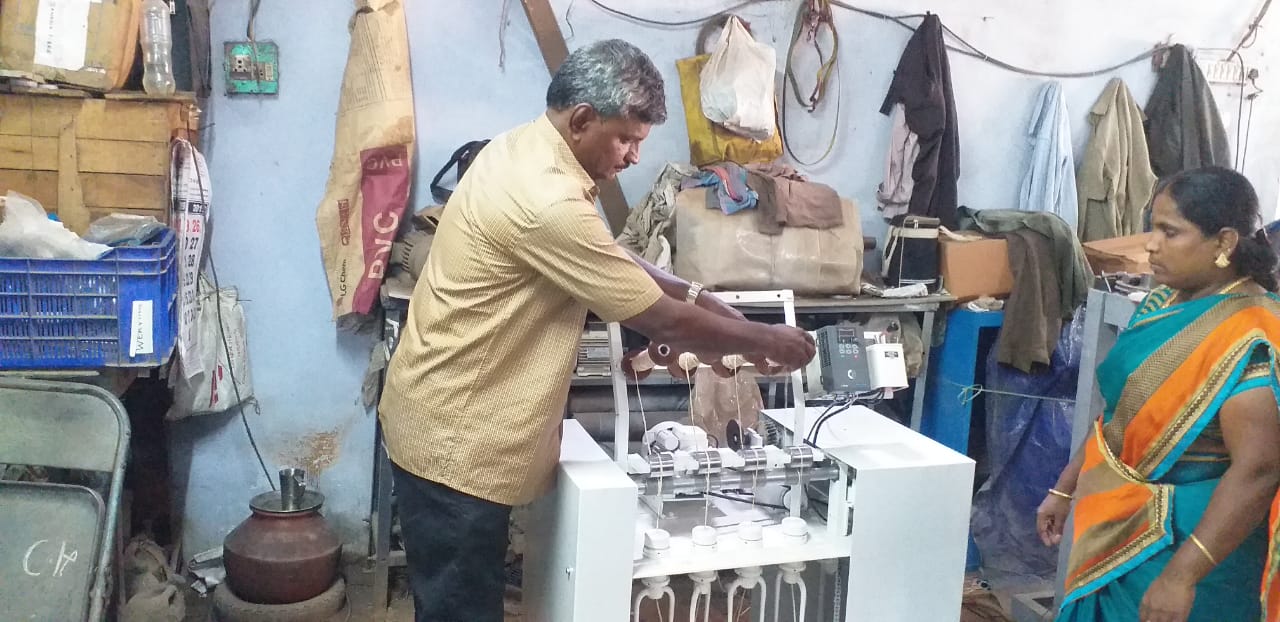
In 2017, Murugesan developed an automated rope making machine, in which a dual function could be performed of making the rope and braiding/twining it together. Murugesan says, “I was using a hand-wheel mechanism to make rope from the banana sheath, and that took five people per wheel for the process, and each wheel yielded only around 2,500 metres of rope. With the new machine, we produce on average 15,000 metres using one machine and with just four people in all.”
The process was slow, but Murugesan is extremely proud of the growth the company has witnessed.
“We started with five people, which grew to 10, then 20, and today we employ more than 350 people, many of whom are women.” The job’s flexibility makes it a great place for women to work in. Murugesan speaks about how many women work from home, take raw materials and make the products. “This way, they can be present for their children, while also earning a decent monthly income,” he adds.
On average, 500 tonnes of banana fibre waste is used by Murugesan’s company annually, and these are used to create a wide range of products.
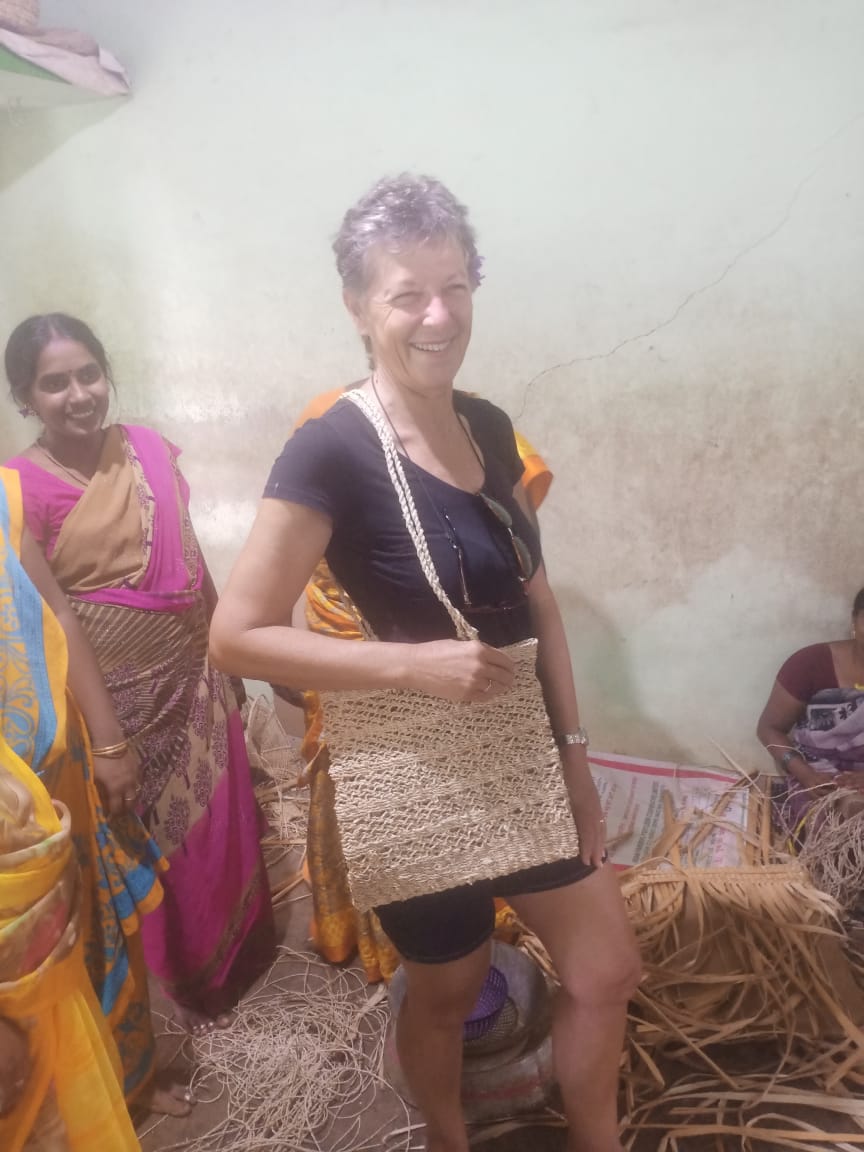
The company makes a revenue of more than Rs 1.5 crores annually, and while most of the products are for the export market, some of the state cooperatives also buy from Murugesan. “We also try and participate in exhibitions held in Tier1 and Tier 2 cities,” he says. Some of the fast-moving products include their woven baskets, bags, and mats. Not just these products, Murugesan has also sold close to 40 machines to various states and organisations, including Manipur, Imphal, Vaishali district in Bihar, Kolar city in Andhra Pradesh and even Kerala.
Murugesan and his team also train the people to work on the machine. He says, “NABARD approached me to make close to 50 machines that will be sent to Africa.”
The recipient of seven National Awards and several State Awards, Murugesan has received the PMEGP (Prime Minister’s Employment Generation Programme) Award from Khadi and Village Industries Commission under the Ministry of Micro, Small and Medium Enterprises, National Farmer Scientist Award from Union Ministry for Agriculture and Best Entrepreneur Award from Krishi Vigyan Kendra at Jabalpur.
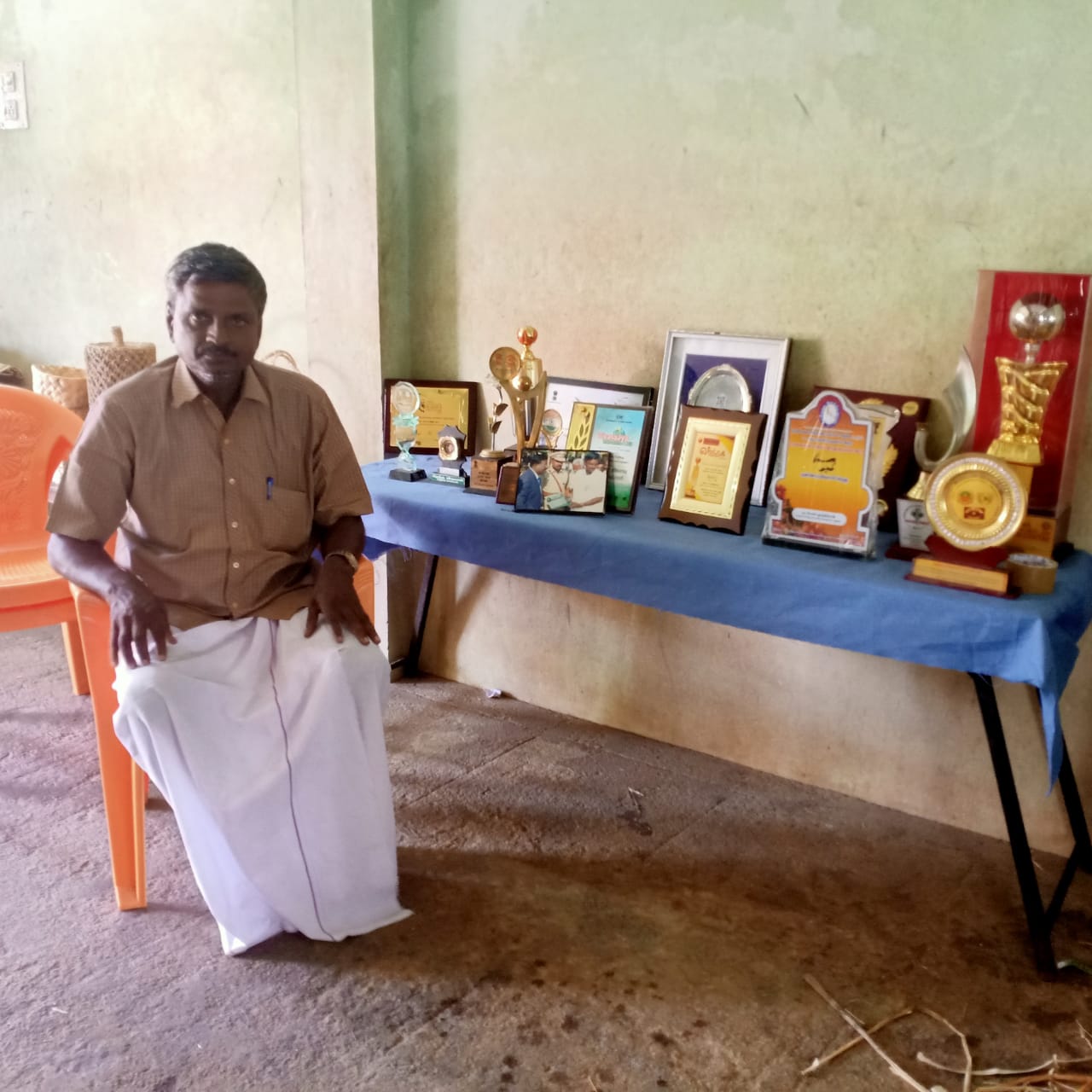
With all these awards in his kitty, what Murugesan is most thrilled about is having brought about wide-reaching change to his village and providing so many people with employment opportunities. “I am a satisfied man. I have managed to get ministers, foreign delegates and people from so many states to come to visit and learn from my small village,” he signs off.
(Edited Yoshita Rao)
No comments:
Post a Comment