Earlier this week, Hindustan Syringes & Medical Devices Ltd (HMD), one of the world’s largest makers of syringes, received an order from the Indian government to supply 265 million auto-disable syringes for the country’s COVID-19 vaccination programme.
Sold under the brand name Kojak Selinge, these auto-disable syringes (AD syringes) are available in different sizes for both mass immunisation programmes (0.1 ml, 0.3 ml, 0.5 ml and 1ml) and general use (2 ml, 3 ml, 5 ml, 10 ml, 20 ml).
(Rajiv Nath, MD of HMD, receiving a jab of Covaxin on the left during the clinical trial, and a representative image.)
This is the fourth order (valued at approximately Rs 55 crore) the government has placed with the syringe-making major. The previous three orders for the 0.5 ml auto-disable syringes totalling to 177.5 million pieces are approaching completion at the end of this month. Supplies for the latest order will continue till September 2021.
“This is in addition to our ongoing global commitments to support global vaccination projects for 0.1 ml and 0.5 ml AD Kojak syringes in developing world whether for Yellow Fever or Measles or Hepatitis B or Pentavalent or BCG, etc. in addition to the COVID-19 vaccination requirements of 0.3 ml for Pfizer’s vaccines or 0.5 ml AD Kojak for AstraZeneca/ Serums or Bharat Biotech’s vaccines,” says Rajiv Nath, Managing Director of HMD.
Considered a safe, easy-to-use, reliable and affordable syringe for mass immunisation programmes by the World Health Organization (WHO) and its partner organisations like United Nations Children’s Fund (UNICEF) and the International Federation of Red Cross, the auto-disable syringe (AD syringe) is designed to be used only once. This eliminates any chances of infection or illness. “Kojak Selinge works on a ‘ring & break’ mechanism which makes sure that the plunger breaks if re-use is attempted,” notes the HMD website.
At present, HMD exports 0.1 ml and 0.5 ml auto-disable Kojak syringes for various global vaccination programmes in the developing world for Measles, Hepatitis B, BCG or Yellow Fever. For COVID-19, the syringe major manufactures 0.3 ml for the Pfizer vaccine and 0.5 ml for vaccines by AstraZeneca/Oxford/Serum Institute and Bharat Biotech.
“India is our priority and comes first but we do have to honour our global commitments and play a balancing role. So, for now we are allocating two-third capacity of Kojak to GoI and one-third to our regular global UN clients,” notes Rajiv.
At the height of the pandemic in June 2020, the Delhi-based company was making about 500 million pieces of 0.5 ml auto-disable syringes per annum. Today, that number has gone up to about 800 million pieces and plans are afoot to expand capacity further to 1.2 billion pieces by September 2021. In totality, the company makes more than 2.5 billion syringes a year, but once again they are looking to expand this figure to about 3 billion by July 2021.
“We sensed a big opportunity in April 2020. We have successfully retooled our existing Dispovan disposable syringes production lines to use them to make Kojak auto-disable syringes. We had to rehire the 1,000 people to replace those who had left us during the onset of COVID and train them with an emphasis on skills and quality consciousness. Fortunately, our technology permits this flexibility of switching between these designs,” says Rajiv.
Each auto-disable syringe costs about 3 cents (approximately Rs 2).
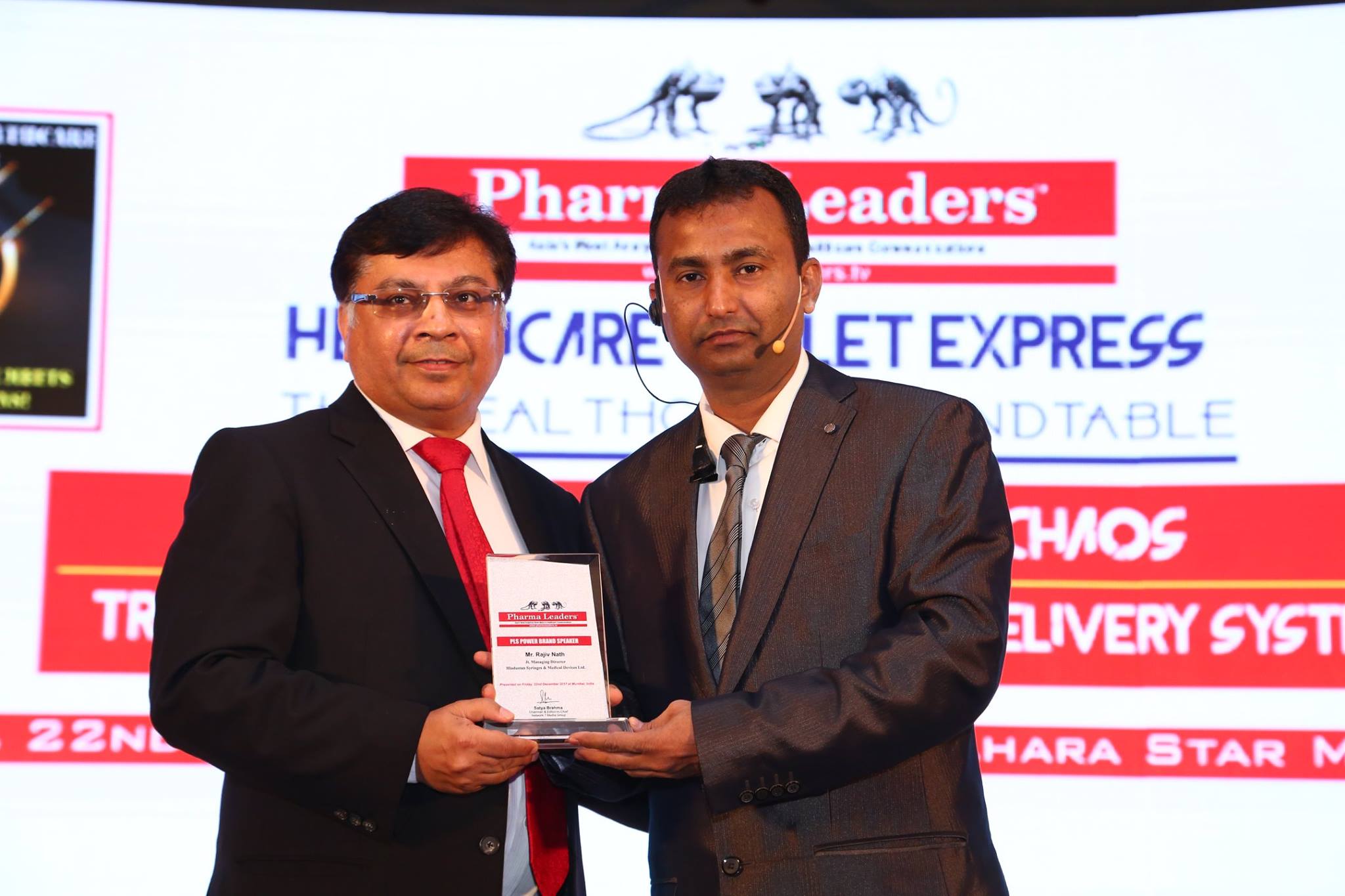
What are vaccines without syringes?
Look up the news everyday, and the conversation invariable shifts to whether countries can secure their share of the vaccine. Unfortunately, not much attention has been directed at whether they have enough syringes to inject these vaccines into people.
Global powers like the United States and the European Union have already gone on record saying they don’t have enough vaccine syringes. More worryingly, countries like Japan have considered throwing away millions of doses of their Pfizer-BioNTech vaccine if it can’t obtain the right kind of syringes.
As per a New York Times report, this is a very important detail: “Not all of the world’s syringes are suited to the task. To maximise the output from a vial of the Pfizer vaccine, for example, a syringe must carry an exact dose of 0.3 millilitres. The syringes also must have low dead space — the infinitesimal distance between the plunger and the needle after the dose is fully injected — to minimise waste,” the report notes.
Experts believe the world needs upto 10 billion syringes for COVID-19 vaccinations alone. Previously, only between 5 and 10 per cent of the nearly 16 billion syringes utilised globally were meant for immunization and vaccination.
For expanding the company’s capacity to manufacture syringes, Nath has made some serious investments. To mass produce these specific syringes even before purchase orders were in sight, he invested about $15 million in May 2020 (approx. Rs 100 crore), which amounts to about one-sixth of his annual sales. These investments included the purchase of new molds from Italy, Japan and Germany to make different kinds of barrels and plungers.
His company manufactures 3.75 lakh syringes per hour at their factories spread over 11 acres in Faridabad industrial district in Haryana. In total, HMD produces over 250 crore assorted syringes a year, although they are planning to scale this up to Rs 300 crore by July.
As the New York Times also reports: “To increase efficiency, Mr. [Rajiv] Nath relies on a syringe design by Marc Koska, a British inventor of safety injections, and its ability to produce all of the components in-house. Hindustan Syringes makes its needles from stainless steel strips imported from Japan. The strips are curled into cylinders and welded at the seam, then stretched and cut into fine capillary tubes, which machines glue to plastic hubs. To make the jabs less painful, they are dipped in a silicone solution.”
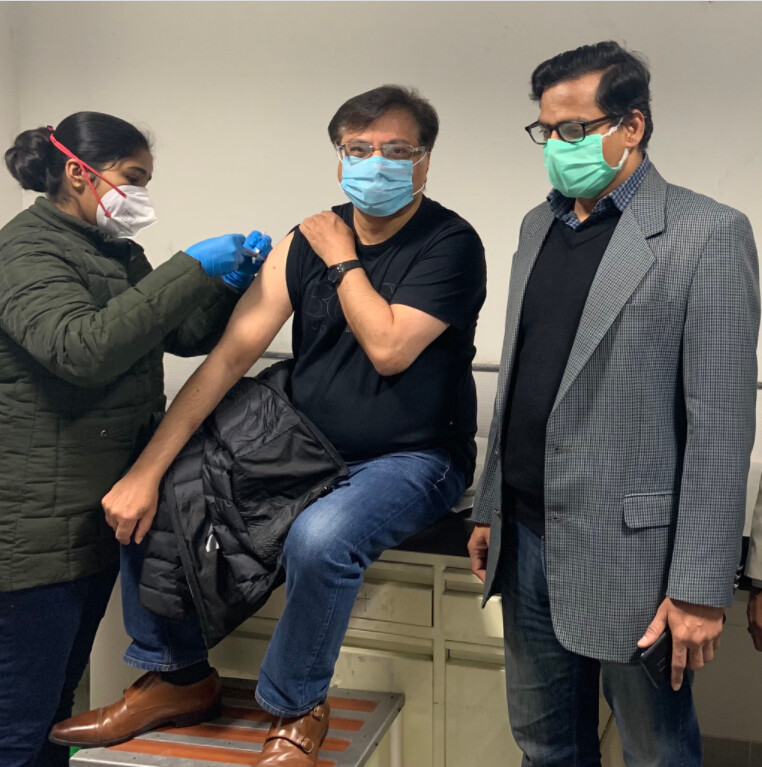
It’s a Family Affair
HMD was founded in 1957 by Rajiv’s father, the late Narindra Nath, who was marked by his passion for redefining the Indian healthcare sector with affordable medical devices.
Rajiv remembers growing up in the cool climes of Mussoorie, where he attended boarding school, until he came back home to Delhi and finished high school at St Columba’s School. Following high school, he attended the PGDAV College, Delhi University, where he graduated with Bachelor of Commerce (Honours) degree.
“There were many hours spent studying books on management and psychology at the varsity’s South Delhi campus. My boarding school and college experience taught me to be street smart, fend for myself without parental hand holding, develop independent thinking and seek innovative solutions to standard problems,” says Rajiv to The Better India.
The objective after college was to join the family business. He had no other aspirations.
“I am passionate about my work and its impact. Thankfully, I am lucky that my hobby, vocation and passion converge at HMD to provide affordable high quality medical devices whether it’s made by us or by the Indian medical devices industry as a whole,” he notes.
Rajiv believes that his company has always been a market leader. “Since the inception of our company, we have always grown with the market from glass syringes to disposable syringes and eventually auto-disable syringes. It’s the same case with needles. We introduced hypodermic metal needles and disposable needles to the Indian market. At present, our share of the Indian market stands at about 60 per cent,” he says.
Until he passed away two years ago at the age of 97, Narindra was the chairman and managing director. In his latter years, Rajjiv was the joint managing director. “We worked as a team and complemented each other’s strengths,” he adds.
Throughout it’s nearly 65-year history, HMD has more or less been a family-owned corporation except for a brief period in 1995 when it needed money to raise production and purchase a lot of new machines. At the time, Narinder sought private capital for the first time.
“We had an injection of private equity when we were going through a very rapid growth phase. But subsequently, we bought back our shares,” recalls Rajiv.
Today, however, the orders keep on coming.
As Rajiv says, “We have received orders for 240 million Kojak syringes for COVAX (the WHO facility maintaining the supply chain of vaccine & syringes for developed nations) via UNICEF and 79 million Dispovan syringes for Brazil via PAHO (Pan American Health Organization) which we are executing side by side. HMD has also recently sold 15 million syringes to the Japanese government. Overall, we serve over 120 countries who depend upon our affordable Kojak and Dispovan syringes.”
He goes on to claim that over 440 million Kojak syringes will be supplied to GoI for India’s massive vaccination drive by September, including 177 million by April this year alongside supplies of Dispovan to private hospitals and vaccination clinics.
Despite these astronomical volumes, the syringe business is hardly profitable.
“This is a very risky business. During COVID-19, it has been challenging to ramp up capacity as the precision engineering demands are tremendous at these high-speeds of production for which our suppliers in Switzerland, Germany Italy and Japan usually take 9-12 months,” he notes. Having said that, it’s homegrown companies like HMD, which give succour to public health systems around the world at this time of crisis.
(Edited by Yoshita Rao)
No comments:
Post a Comment