Ipower Batteries, a Delhi-based startup, reached an annual turnover of Rs 50 crore in the Financial Year (FY) 2020-21, despite the hit their business took during the pandemic.
(Image above Ipower MD and Founder Vikas Aggarwal on the left and his facility on the right.)
Manufacturing and supplying lithium-ion battery packs for different electric vehicle (EV) companies including Gemopai, Benling India, Okinawa Autotech and Ampere Electric, the Delhi-based startup serves 15 of the top 20 EV two-wheeler makers in the country. Cumulatively, they make lithium-ion battery packs for approximately 100 Original Equipment Manufacturer (OEMs) across two, three and four-wheeler (L5 Category) makers that are tailor-made to their specifications and requirements.
Apart from battery cells, which Ipower imports from Japan, South Korea and China, everything else is designed and made in-house thanks to their Central government-approved research and development (R&D) facility. However, it has only been three years since the startup began manufacturing lithium-ion battery packs.
“In the EV segment, we began our journey in 2011 supplying lead-acid batteries to OEMs making low-speed two-wheelers like Hero Electric and their retailers and distributors across India. However, we stopped making them because lead is a serious health and environmental hazard as well. In the past three years, we have switched gears from lead-acid to the more efficient lithium-ion, for which we have an in-house government approved R&D laboratory. There we design and develop the battery technology best suited for the Indian environment, geography, [high temperature] climates and consumer requirements such as seeking greater mileage and cost efficiency,” says Vikas Aggarwal, Founder and Managing Director of Ipower, speaking to The Better India.
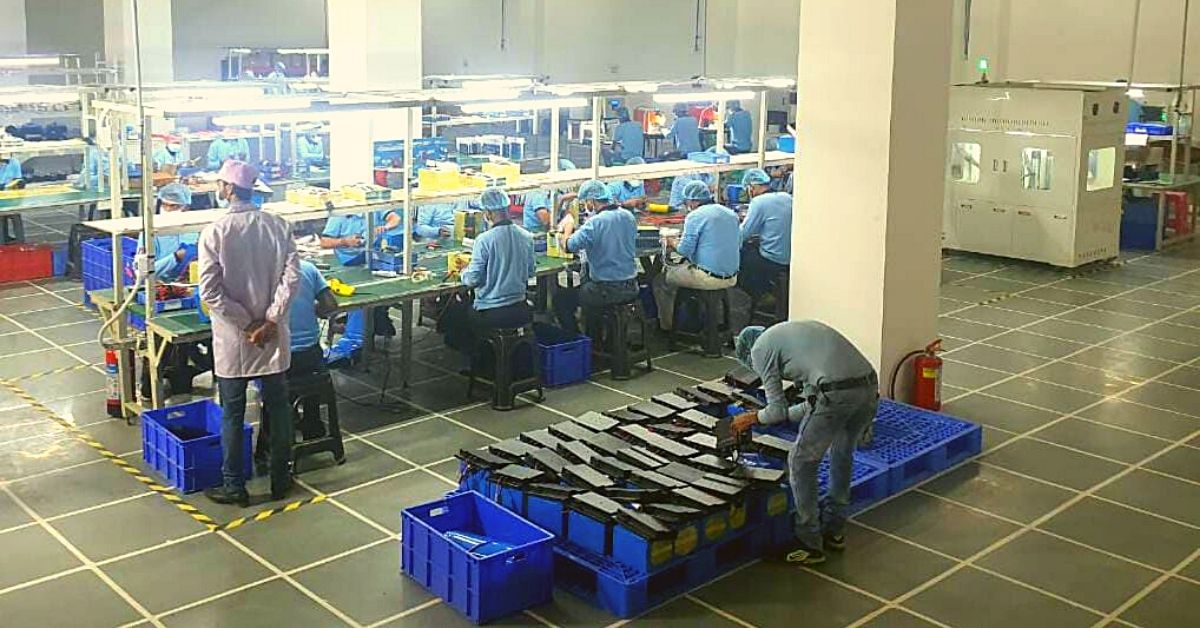
Making EV Batteries for India
It was only in April 2020, when Ipower broke away from its parent company, Computech Systems, which is in the business of making UPS systems, SMF (Sealed Maintenance Free) batteries and laptop chargers, among other products. Established by Vikas’ father, the late RC Aggarwal in 1992, Computech Systems was steadily moving along in its business when in 2011 they decided to diversify into the nascent EV sector with the Ipower brand name.
“So, I took up the trading of lead-acid batteries for OEMs in a very nascent Indian EV market. The objective wasn’t merely to make money but add value to the country by reducing vehicular pollution, massive import bills from buying fossil fuels from foreign nations, etc,” he says, recalling, “Growing up, I also had a fascination for EVs and always wanted to get into this business in India.”
He adds, “This transition to EVs began in 2011, although we were still focussed on Computech Systems as well. Until last April, Ipower was a subsidiary of Computech. Today, they are separate companies with Ipower completely focussing on making lithium battery packs for EV startups and companies.”
Today, the company’s state of the art lithium-ion battery packs are popular among EV startups as they are swappable and modular. These battery packs also come with advanced tracking, geo-fencing, remote monitoring, battery immobilisation, active and passive cooling and control, among other interesting features.
The process of making these battery packs happens in their 50,000 square feet manufacturing facility in Kundli, Haryana, where they have also set up the infrastructure needed to test and validate their products.
“Our facility can manufacture about 500 battery packs per day, although we are presently making about 200 battery packs. Since the onset of the pandemic, a lot of consumers are shifting away from public transport to private vehicles. There is a huge demand from EV startups and companies for batteries,” says Vikas.
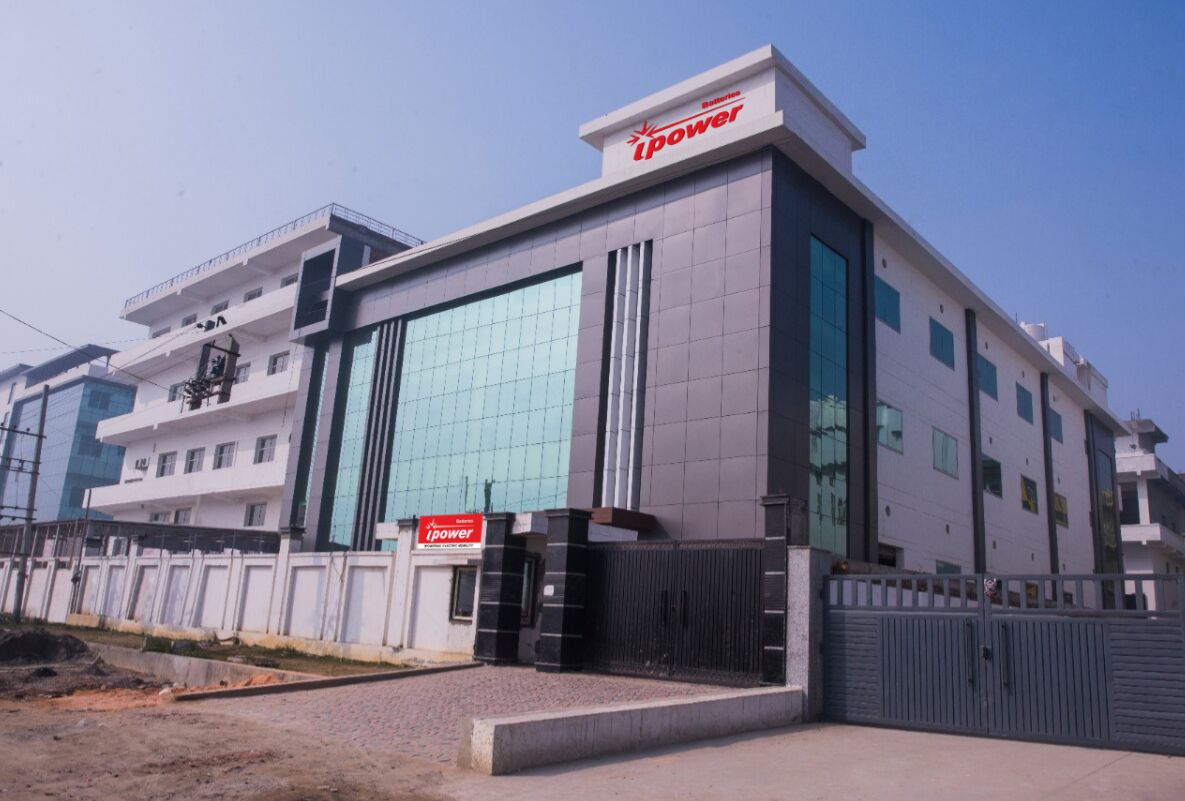
The Process
Ipower conducts the R&D in-house after selecting the best in the class battery cells. The company has also employed experts situated in companies abroad that manufacture battery cells just to test them before they are dispatched to India. Once the cells arrive, they store them in a facility where the temperature is maintained at 25 degrees Celsius and test them once again. There is a defined process of how the startup manufactures battery packs where it is tested at every level for quality assurance.
“The cells are first graded and sorted in terms of voltage, internal resistance and capacity. After the sorting process, we make a module of the battery pack, perform spot-welding in the module, solder it with the BMS and here a soft pack is made. Every battery pack is tested for quality assurance. There is no random testing. We then put in the soft pack for final assembling which is subsequently done. After final assembling, these packs are covered in complete battery enclosures made of metal, aluminium or ABS (Acrylonitrile Butadiene Styrene – a non-conductive high impact resistant thermo-plastics), depending on the customer requirements to protect the battery pack in case of a crash, fire or any other emergency, following which there is another end of the line testing,” explains Vikas.
This is roughly how the manufacturing process takes place. For the company, maintaining the safety parameters of battery packs are paramount. After the final end of line testing, they ship these battery packs to buyers in safe containers to ensure no damage during transit alongside their detailed testing reports.
Vikas notes how a majority of the battery packs they sell are in the 1.5 to 2 kWh range for two-wheeler manufacturers. These batteries make up about 60 per cent of the total demand for Ipower’s batteries. For three-wheelers, they make 5 kWh lithium-ion battery packs and 10 kWh packs for four-wheelers (L5-Category). Both these segments make up a further 20 per cent of the total demand for Ipower’s batteries, and the rest is covered by e-bicycle makers.
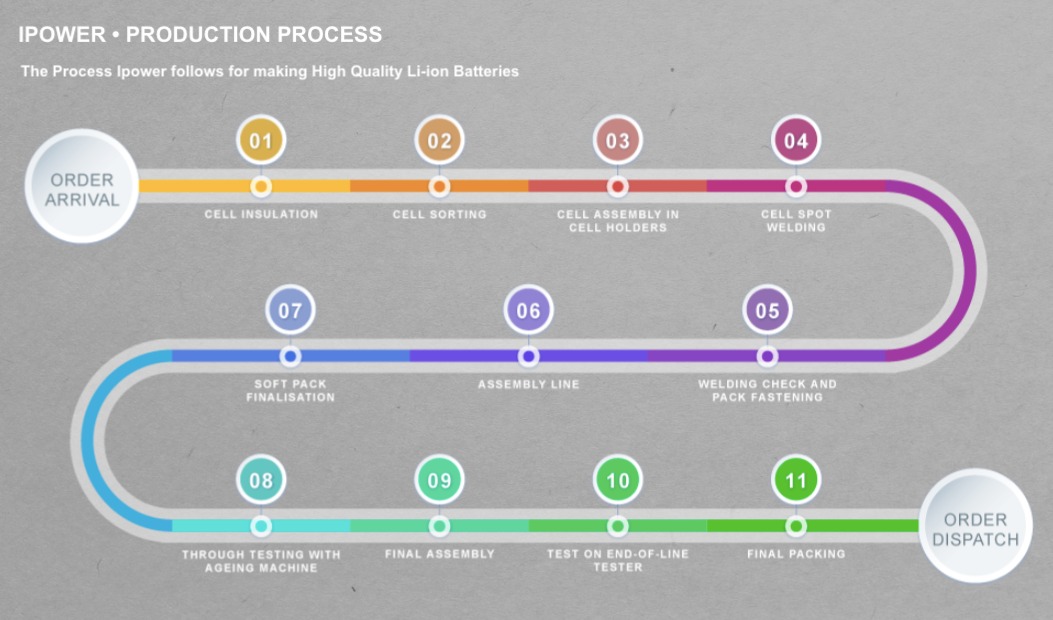
Addressing Challenges and COVID
As battery manufacturing for EVs was still in its nascent stage back in 2019, Ipower’s workforce was not initially skilled enough to make lithium-ion batteries for Indian conditions.
“In other words, we struggled to find people with the necessary technical expertise to develop the right sort of product. We had hired some skilled personnel from overseas to help train our workforce. We also sent our team to visit international battery factories to learn how to make high-quality battery packs. Through all this, the workforce also learnt how to make the right sort of product keeping in mind cost optimisation, safety and range,” he says.
The next challenge was to ensure the safety of their battery packs. Lithium-ion batteries can prove dangerous if mishandled, and there have been reports in the past of vehicles catching fire.
“Extra care was needed in designing the battery pack because of concerns that people’s vehicles were catching fire. We were determined to ensure Ipower’s batteries were equipped with an extra layer of security, while also constantly explaining to our dealers the safety guidelines. Ensuring safety is the most important facet of our manufacturing process. Also, since we are essentially a startup company, funds are required particularly for the R&D process which ensures greater and safer product quality. It’s a costly affair,” notes Vikas.
Even though lithium-ion batteries are more efficient than their conventional lead-acid counterparts, it has been a challenge to make these packs cost-effective. Thankfully, subsidies and initiatives by Central and State governments have helped in this regard.
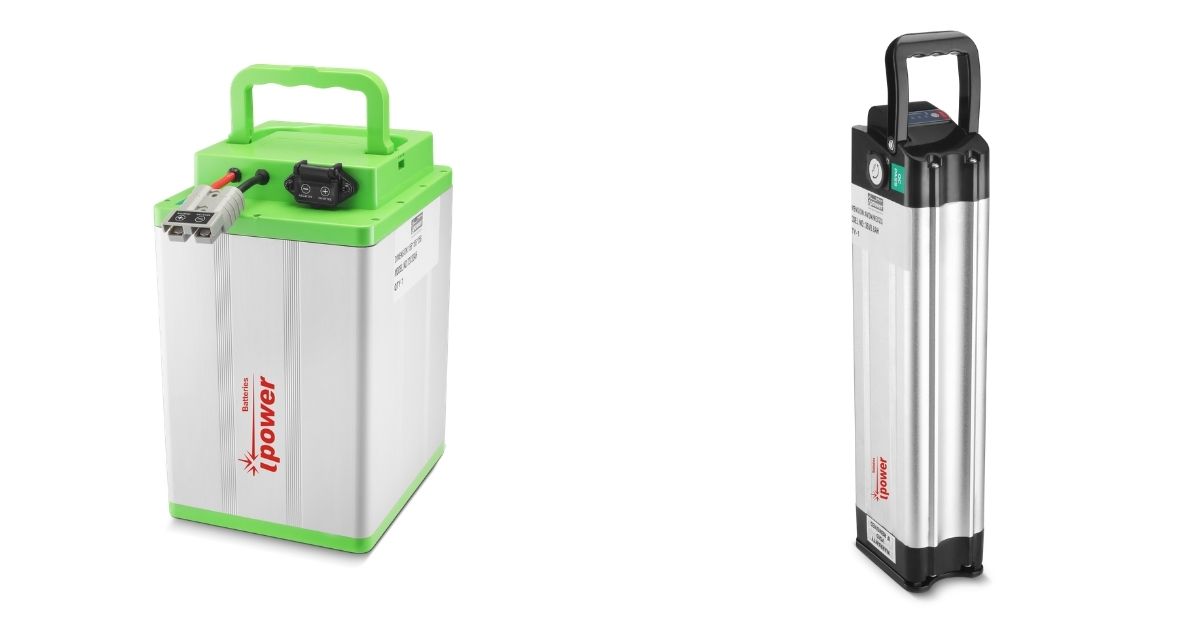
Last March, of course, the nation confronted the deadly COVID-19 pandemic. During the first lockdown, the business took a significant hit with sales down by 60 per cent in July. Despite real concerns, they focussed more on conducting R&D, and after a couple of months, their business bounced back to pre-Covid levels. With the second wave raging through these past few weeks, they’ve had to shut down their facility for days.
“We haven’t laid off any of our 200 employees in the company. Also, since we have ample space in our factory, we can safely maintain social distancing, while enforcing mandatory mask-wearing. Every Saturday, we set up a COVID-19 testing camp in our plant. Our employees can get tested once a week free of cost. We fumigate our factory three times a day when our employees take respective breaks. We have been fortunate that there have been no COVID positive cases in our factory so far,” claims Vikas.
With an emphasis on R&D and retraining their workforce to make lithium-ion battery packs, the company didn’t make major net profits in the early years. Meanwhile, this time around, the pandemic has hit the business, but there is hope that once the second wave subsides, they can catch up and attain a turnover between Rs 80 and Rs 100 crore for FY 2022.
(Edited by Yoshita Rao)
No comments:
Post a Comment