In May 2020, as India grappled with the second wave of COVID-19, Pabolu Mohan Aditya, a mechanical engineering student at SRM University, Andhra Pradesh, came across people who could not afford protective medical gear. He saw policemen in his neighbourhood with just a simple face mask having to work for over 12 hours every day to ensure COVID-19 restrictions were followed. Watching them at work, despite a serious threat of infection, he was determined to create a face shield that is affordable and easily available.
“During the start of the pandemic there was a huge demand for protective gear like PPEs, masks and face shields but because of the pandemic, supply chains all over the world were disrupted, leading to high prices for the limited gear available. That’s when I decided to do something to help,” the 21-year-old shares with The Better India.
At the same time, he was determined to create an alternative that would not add to the pollution that plastic waste was creating due to the pandemic.
Research shows that face shields, in addition to wearing masks, are up to 98 per cent effective in preventing the spread of the virus. However, another study confirms that approximately 3.4 billion single-use face shields have been discarded daily as a result of the pandemic.
With these considerations in mind, in April 2020, he began working on an eco-friendly design for the face shield.
Being a mechanical engineering student, he used computer programming and product design to come up with an eco-friendly prototype. With the help of his family, he then approached a manufacturing company near his house to use their machinery for the production of the mask.
After testing the prototype on friends and family, he began distributing them to frontline workers such as doctors and police officers in the city. He also approached his teachers at college to get feedback and improve the design.
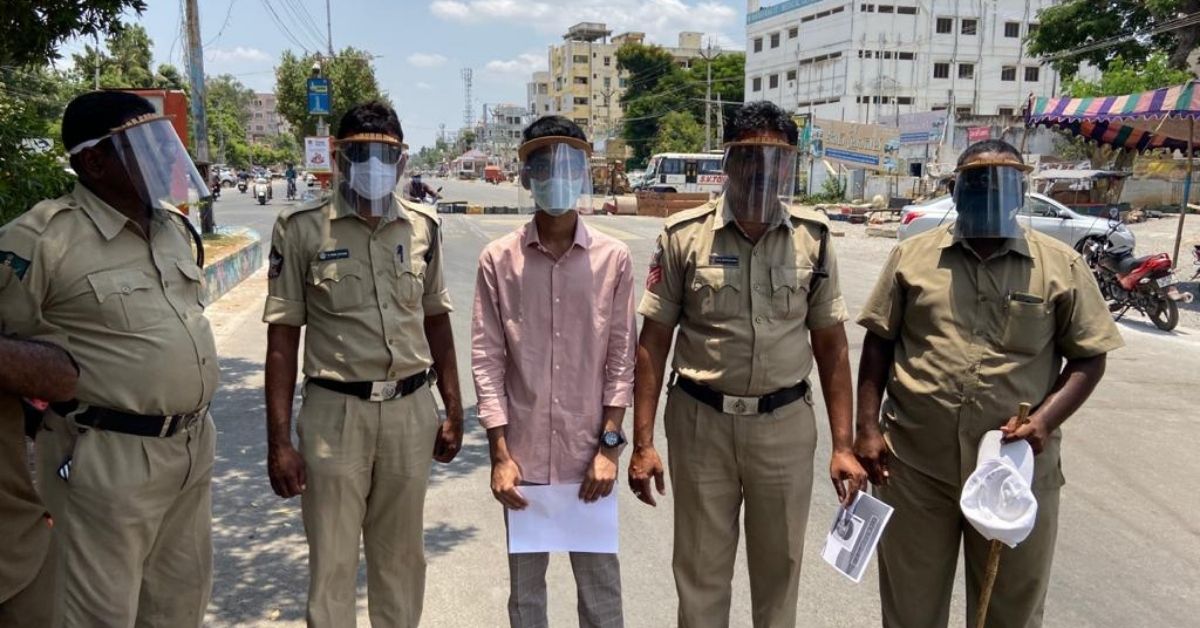
Durable, reusable and biodegradable
At first glance, the face shield looks similar to the plastic ones found in the market but it has several other benefits too. It consists mainly of three parts — the headband, the protective film and the elastic thread to hold the headband.
The headband is made using 3-ply corrugated cardboard, which makes it durable, lightweight and easily degradable. Additionally, the front of the headband is frayed which makes it easier to wear. The shield also comes with an elastic thread so that the headband can fit different sizes and is adjustable. This makes the face shield comfortable to wear over long periods of time.
The transparent visor is made of a thin layer of 175-micron reusable plastic and is equally effective as the existing plastic face shields. To produce the visor for the face shield he used specific software.
“I designed the transparent film for the visor using computer-aided design (CAD) software and manufactured the headband by inputting the CAD model in the computer numerical control (CNC) machine. This machine cuts the cardboard and transparent sheet into the required design and then the product is assembled,” Aditya explains.
In addition to all the materials being biodegradable, the shield comes with an interlocking mechanism, which increases the lifespan of the product.
“In case any component of the shield, say the headband, gets damaged, this mechanism allows one to detach the protective film from the headband easily and reuse the film on a new headband. This helps increase the lifespan of the product and helps reduce the waste generated,” the young innovator says.
What it takes to win a patent
In June 2020, on the advice of the college administration, Aditya applied for a design patent so that he could commercially produce the biodegradable face shield. He took out time to learn the process and conditions to apply for the patent and was supported by the attorney of SRM who answered all his doubts.
“It is quite tough to get a patent. Until last year, I was completely unaware of what it meant. Patents are granted for products that fulfil specific requirements like novelty as well industrial application, so I made sure my product has all these features that set it apart from existing products,” says Aditya.
While the existing face shield costs around Rs 150, Aditya’s shield costs only Rs 15. Moreover, the time taken for its production is less than two minutes and it is cost-effective. “I had heard of methods like 3D printing being used for producing face shields but in a country like India, this is not feasible as it is expensive and takes a long time to manufacture one face shield,” he says.
The entire face shield takes about three months to decompose thus helping combat plastic pollution.
After waiting patiently for over a year, in May 2021 Aditya was awarded a design patent for his eco-friendly face shield.
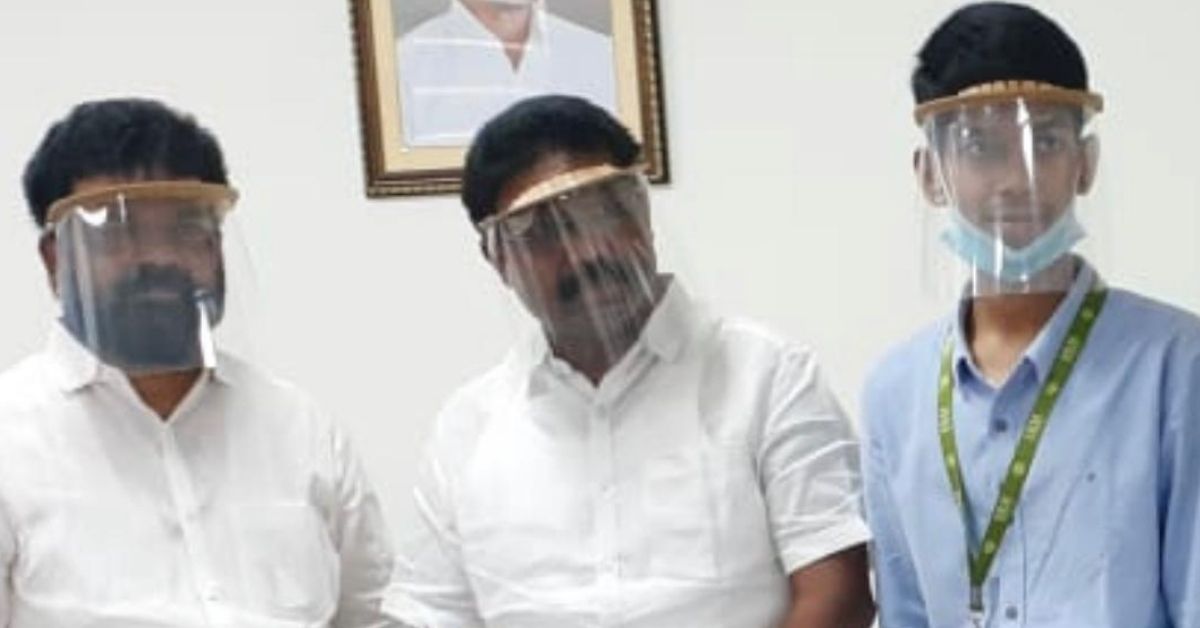
So far, he has made and distributed 500 shields to cops and more than 150 to doctors across the city. He plans to begin commercially manufacturing the face shields in the coming months.
The face shield is not his first shot at creating an innovative product. Aditya, along with some friends, had previously converted a 10-year-old internal combustion bike into an electric vehicle. He is currently working on creating beds for COVID-19 patients using reusable materials — a project he calls “building blocks for beds”.
“The pandemic has taught many of us how to think out of the box and come up with unique solutions. It is extremely important for people to continue to innovate and discover new solutions so that we can bring about a change in society,” concludes Aditya.
Edited by Yoshita Rao
No comments:
Post a Comment