In the early 2000s, a unique technology was making headlines for being a possible solution to the perennial problem of plastic waste. This technology could prove to be a game changer in how we manage our waste and a counterargument to blanket bans.
The woman behind this technology was Nagpur-based Alka Zadgaonkar, former professor and head of department of applied chemistry at Raisoni College of Engineering. While working in her lab, Alka discovered a technology to convert plastics into fuel without causing pollution. This could include plastic waste of any kind — broken buckets, pet bottles, tetra paks, eWaste or plastic bags.
However, a few roadblocks along the way resulted in Alka and her technology retreating from the public eye. Now, as we gear up for World Environment Day on June 5, Alka and her husband Dr Umesh, along with Pankit Mehta, in charge of their marketing and development of the plant and machinery, tells us about the technology, the inspiration behind it and how they feel this endeavour can be scaled up.
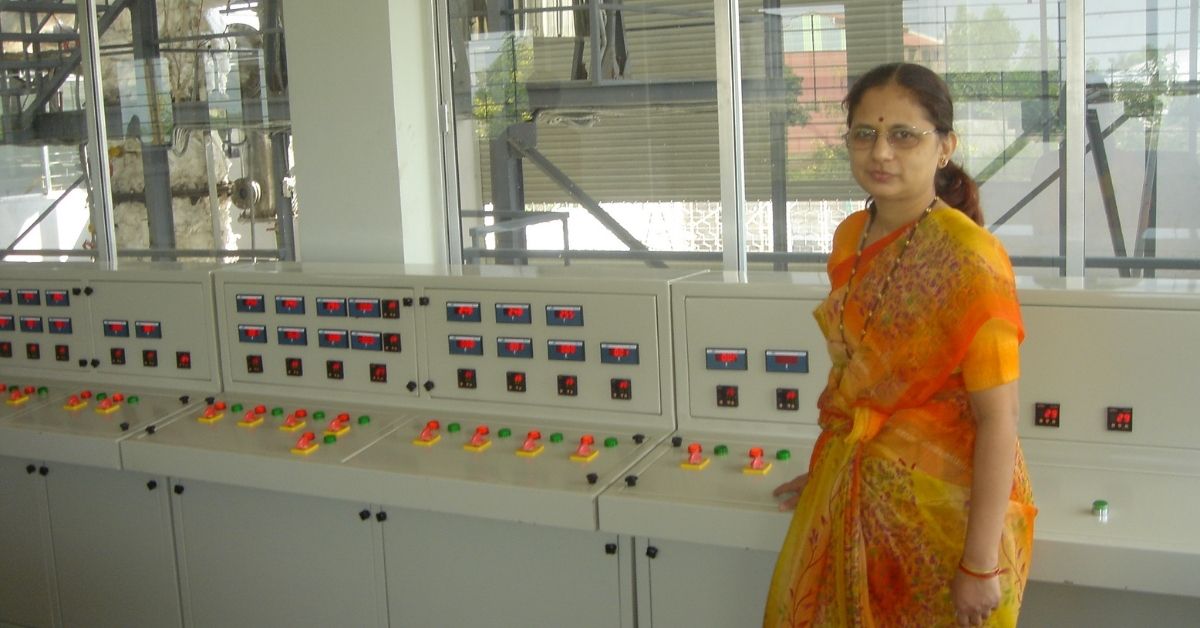
‘You can’t do away with plastic’
“Plastic is a versatile compound and its usage across industries and sectors is vast. But the plastic wastage problem is even bigger. During my days teaching engineering students at Raisoni, one thought that stuck with me was that this material finds its origin in crude oil. Plastics are made with polymerisation, so I thought that if we could use de-polymerisation to transform it back into its origin, we could work around the problem of wastage,” Alka, now 59, tells The Better India.
Alka shared this idea with her husband, Dr Umesh, who she credits as being her biggest support. “He encouraged me to dig deeper into this idea. I worked with different reactors of small capacities and eventually scaled from there,” she says. “My role was till the creation of this technology, but my husband scaled it up eventually to take it to a 5-metric tonne plant in Nagpur.”
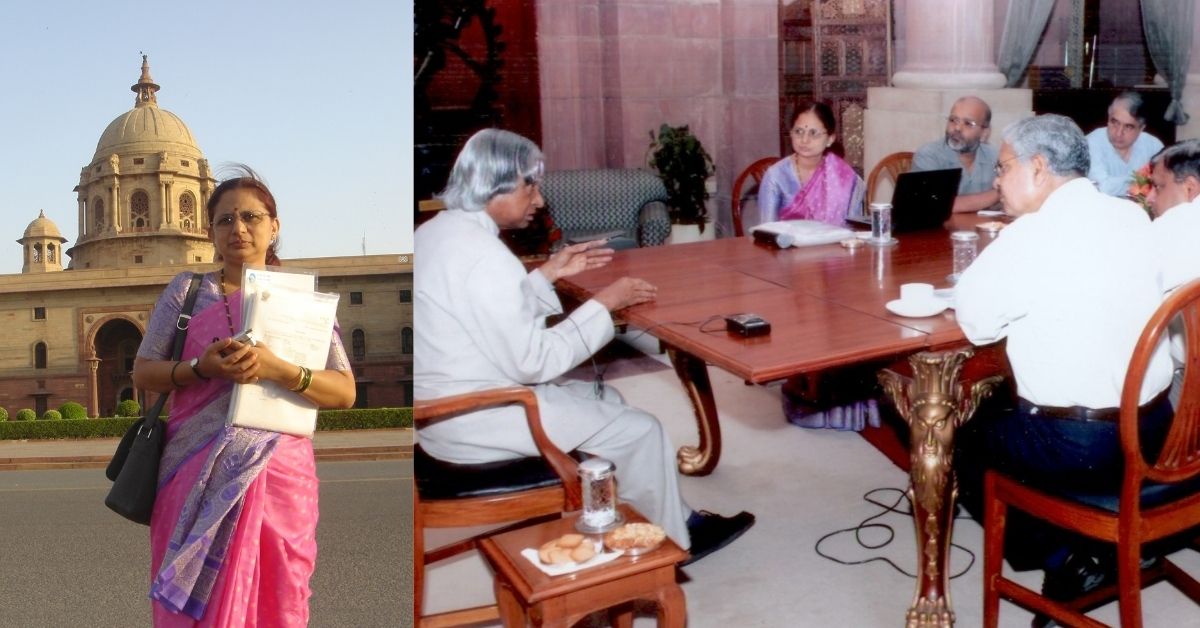
During the 90s, Alka began noticing piles of plastic around her otherwise clean city. Big cities by this time had already begun to feel the brunt of discarded plastic waste and the discourse around finding a viable solution was gaining traction. However, she says the idea was also formed upon the realisation that bans on plastic are not the solution. “There are many forms of plastic, other than just bags, that we use in our daily lives. A blanket ban on plastic will not solve this issue,” she notes.
Currently, India generates around 3.3 million metric tonnes of plastic waste annually. Even if we look back on states and UTs that have imposed plastic bans as early as 1998, we would see that the generation and consumption of plastic have only increased up until now. In 2018, when Maharashtra imposed a ban on the “manufacture, usage, transport, distribution, wholesale and retail sale, storage and import” of plastic, the move invited the appreciation of environmental activists, but alongside came the wrath of producers, retailers and shopkeepers who use plastics as packaging. Outright bans have seldom proven to be effective. Instead, what is needed is alternative material and means to such stakeholders, as well as better technologies to recycle and manage waste.
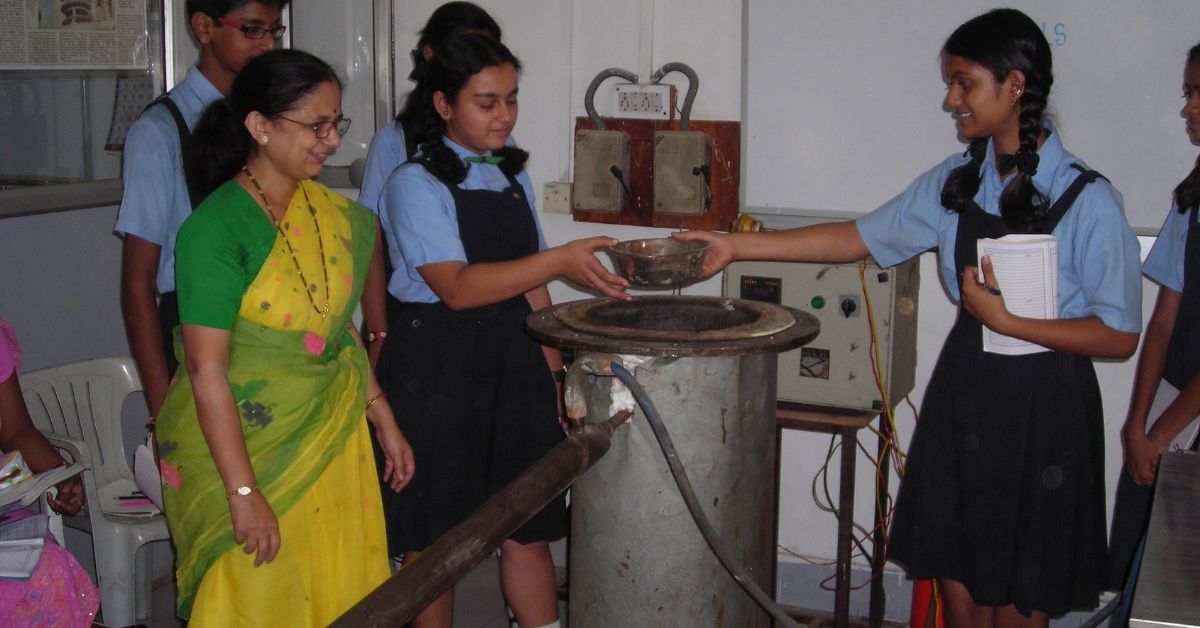
A new alternative to waste management
This was the same thought that Alka kept in mind when she invented her technology. It essentially involves depolymerisation rather than pyrolysis, which efficiently breaks down the molecular chain of plastics and converts the material into hydrocarbons. It uses a lower temperature, 375°C, as opposed to 600°C in pyrolysis, thereby producing a better energy to efficiency ratio, alongside reducing costs of production and increasing profits. The wax formation in this process, as compared to 15% in pyrolysis, is only 5%, leading to minimal clogging of key components and thus reducing the costs of cleaning and maintenance. According to Mehta, the quality of oil due to the absence of wax is better and uniform coke formation results in easier removal, thereby reducing the time between batches.
Dr Umesh says, “This is a closed-loop process. We don’t emit anything into the atmosphere. We produce around 70-75% of liquid fuel, 15-20% gas and the rest is coke. Various plastics will give you various proportions of output.”
The news of Alka’s invention gained media traction and in 2003 the Indian Oil Corporation’s R&D Department approached the couple. They conducted a few demos which proved to be successful, and declared possible end-users of this fuel — for liquid hydrocarbon, agricultural pumps, DG sets, boiler fuel, and marine bunker fuel; for gas, industries using LPG and in-house consumption; and for solid fuel: thermal power plants, and use in metallurgical industries. The couple was given a grant of Rs 6 crore for a pilot production plant to be set up by the Zagdaonkars and the IOC.
However, this grant never came through. The Zadgaonkars instead found themselves in a whole bunch of litigation, with a few stakeholders vying for equity and co-inventorship. So in 2004, Dr Umesh took the technology to the State Bank of India, who put their trust in this nascent technology and granted the Nagpur residents a loan of Rs 5 crore. In 2005, a plant was set up in Nagpur. However, the couple found themselves buried in legal battles for around 12 years.
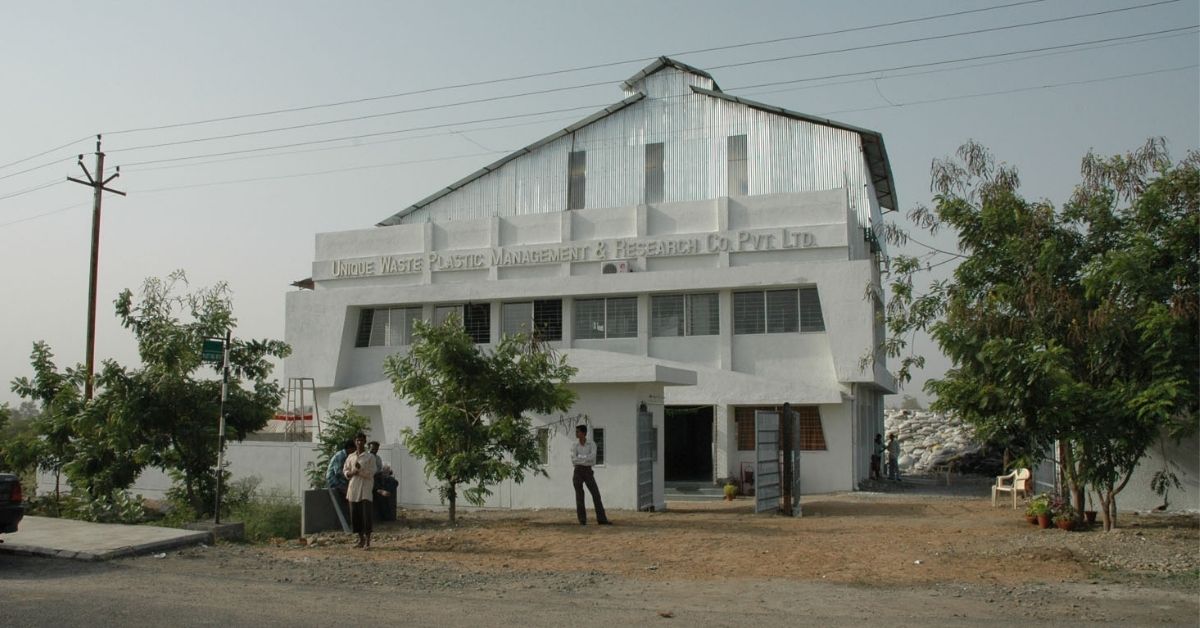
The plant began with a capacity to convert around 5 tonnes of plastic per day, and currently, this has been scaled up to 10 tonnes. Before the pandemic, the Nagpur plant was selling 5,000 litres of fuel to nearby industries. In 2018, the plant was shifted to Mumbai on the behest of the Brihanmumbai Municipal Corporation (BMC).
Mehta, who takes care of the commercial side of the business, says, “I handle all marketing and development of plant and machinery.” He adds, “The Zadgaonkars invented the catalyst and had done certain R&D on what we call a kilo-level technology. My role has been to upgrade it from that kilo level to the tonne level. I joined the company in 2012 when they were coming out of various litigation.”
The road ahead
By 2015, Mehta and the Zadgaonkars had worked to build reactors with greater capacity. “We looked for heaters and burners that are completely pollution-free. We took months of R&D and customised our heaters to remain in line with the PCB guidelines. From January 2018 till August 2019, we ran the plant daily in Nagpur and converted between 5 and 10 tonnes of waste. We began marketing the technology and were then approached by the BMC.”
He adds, “The BMC wanted the plant and machinery on an immediate basis and for free. We accepted the terms and conditions but convinced them to let us shift the Nagpur plant to Mumbai, which would be cost-efficient and save time as well. We planned to start production by November, but around that time, there were political splits in Maharashtra, and our inauguration was postponed. Eventually, a soft inauguration was done in March 2020 by former BMC commissioner Praveen Pardeshi, but almost immediately after, the COVID-19 pandemic hit and the picture changed again.”
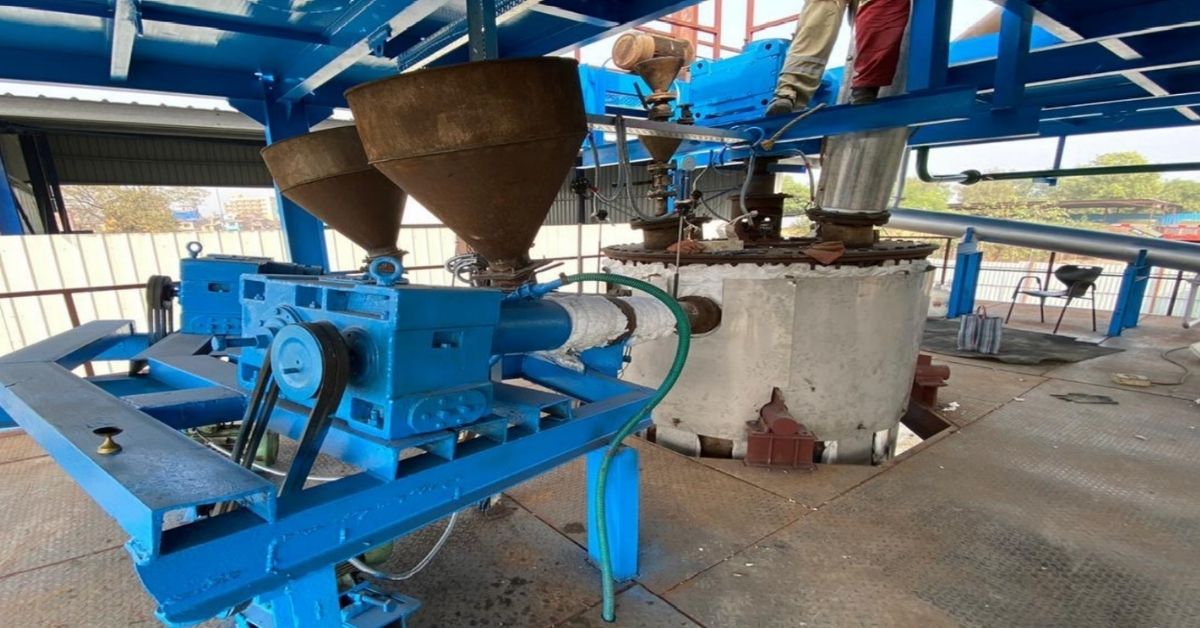
Why then has this technology, which can provide a pollution-free solution to managing India’s large scale plastic waste, not achieved more prominence?
“In our case, we invited a lot of problems due to over-publicity. The amount of litigation we faced put things on hold for us for several years, which is why we could not move forward with our idea. If you search about this technology on Google today, you might get thousands of results. But unfortunately, not many of these plants are working,” Dr Umesh explains.
Meanwhile, Mehta says, “There are many people who are working on this globally. The difference here is that their technology employs pyrolysis, which is extremely polluting. Our process involves polymerisis, which also makes a difference in the quality of oil. We didn’t want to make the same mistake. Our idea was to iron out all the R&D and make sure we were marketing as much as we could sell. I do get inquiries about selling our plant and machinery, but I don’t want to sell a half-baked product and spoil what the Zadgaonkars have built. The answer lies in adequate research, as well as the quality of oil in the market.”
After spending years fighting tiring legal battles, the Zadgaonkars have retreated to a low-profile and peaceful life in Nagpur. But their contributions to pioneering the solution of plastic waste management can certainly not be overstated.
Edited by Yoshita Rao
No comments:
Post a Comment