In 2016, K Deepak Reddy graduated with a degree in mechanical engineering from Hyderabad and returned to his native village Borancha in the Sangareddy district of Telangana.
One day, while out and about on errands, he came across a vast farmland that was lying vacant. “The land areas had been empty since my childhood days. When I started making frequent visits to the area, I realised that no crops had grown there for years,” he says.
Deepak tells The Better India that he asked farmers nearby why hundreds of acres of land had remained barren for years, and was told it was due to the large amounts of stone debris, which had made it unfeasible to carry out any farming activity in the area.
“I also learned that removing stones from the land required huge expenses, and marginal farmers with 5-7 acres of land could not afford to spend thousands of rupees for the task, in addition to the investment required for agricultural activity,” he explains.
Moreover, even if the farmer is ready to invest that kind of money, removing these stones and rocks from the farmland demands at least five or six years and recurring costs. “The surface layer has 60% of the stones. However, it takes another few years to remove the rest via multiple cycles of seasonal ploughing and tilling of the land,” he says, adding that this activity can only be conducted during summer months, when the soil is dry.
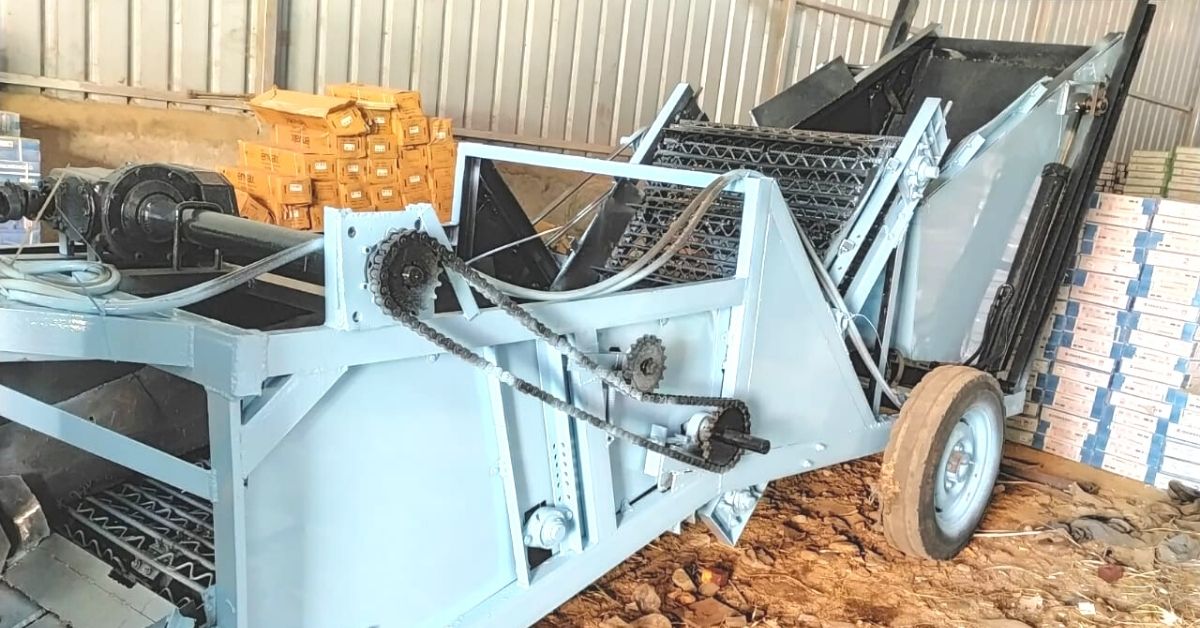
When he researched further about the terrain, Deepak realised that thousands of acres of barren land had remained unused across nearby states of Maharashtra, Karnataka and Andhra Pradesh. “Other countries also face this problem, but they have mechanised solutions. In India, there was no cost-effective equipment for the task,” he notes.
So he built a low-cost multi-harvester machine for farmers, which not only digs out stones in a matter of hours, but also harvests potatoes, onions and other root vegetables.
Simple, yet effective
Deepak says that after his graduation, he was upgrading his skills by learning simulation and software design. “I decided to use the skill and develop a machine that could be attached to a tractor and thus remove stones from the upper layer of soil as well as underneath,” he adds.
The 26-year-old says that he worked for years to build the harvester. “My idea was to build a machine that is suitable for Indian farmers. It needed to be low-cost with basic features. However, I thought that if it could also harvest potatoes and root vegetables, it would add value to the machine,” he says.
Deepak says he worked on a concept where the equipment is attached to and pulled by a tractor moving forward. “The blade attached at the bottom of the machine digs the soil to fish out stones and drops them onto a conveyor belt. The net structured belt system rotates along the axis and, in the process, filters the soil, dropping it back on the ground. The stones remain on the conveyor and are transferred to another belt for the second filtration stage, segregating the remaining soil. After that, the stones are collected in a storage bucket,” he explains.
He adds that the same principle applies to potatoes and other root vegetables.
The multi-purpose harvester is not only cost-effective but also efficient in terms of the time and effort required. “A farm labourer charges Rs 5,000 and spends an entire day removing the stones from an acre of land. However, my machine can accomplish the task in a matter of four hours, at the cost of Rs 1,500 per acre,” he says.
Deepak says efficiency is a crucial factor for farmers, as the machine makes harvesting vegetables easier and quicker. “The earlier the farmers reach the market with their produce at the beginning of the season, the better the profits,” he adds.
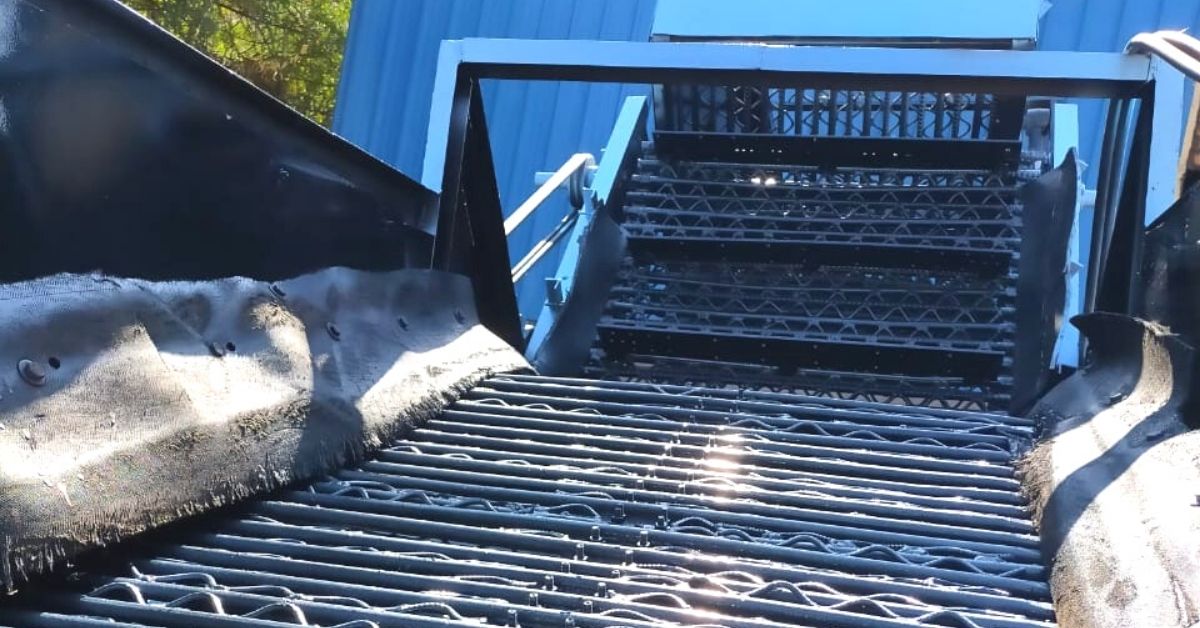
The engineer has succeeded in converting a 5-acre rocky terrain into cultivable land and aims to cover 500 acres by selling 25 units next year.
Santhosh Rajput, a farmer of Kangti village in Narayankhed district, says he has taken a trial of Deepak’s harvester, and that it works wonders. “I have 30 acres of land, but can only farm on 15. The remaining have rocks and stones. Even if I attempt to grow crops, the stones heat up during peak summer days and kill the plants due to the high temperatures,” he says.
Santhosh says another farmer in the village imported a similar machine from Turkey, which cost him Rs 12 lakh, but failed to deliver satisfactory results. Meanwhile, Deepak’s machine is much more efficient, yet costs Rs 3 lakh, he notes. “Many farmers can collectively buy it or rent it for temporary usage,” he adds.
However, developing the machine was no cakewalk for Deepak, and it took him four years to come up with the final model. “I had no friends or team to work with or share ideas. I worked alone and solved all the issues single-handedly. Moreover, I had no financial back-up and borrowed Rs 4.5 lakh from family and friends,” he says, adding that he knew that if the product became a success, the financial issue would sort itself out.
Deepak says that earlier, he worked under a tree at his family farm and had no workspace. Later, he moved to a makeshift space in a friend’s garage.
Helping the farming community
“I achieved 90% success with my fourth prototype and applied for the Telangana State Innovation Cell and Make Room India’s initiative, i2E (innovation to entrepreneurship) lab. The mentors guided me to create a commercially viable product and helped me receive a grant of Rs 10 lakh from NIDHI Prayas, thus allowing me to launch my startup Bhaumya Innovations,” he says.
Deepak’s mentor, Pranav Hebbar, founder and head of Make Room India, says, “The programme aims to identify entrepreneurs like Deepak, particularly from tier II and tier III cities, who have the potential to solve problems at the grassroots.”
Pranav says, “Rough estimates show that about 1,000 acres of land in Sangareddy, Medak, Kamareddy and Nizamabad area alone have stone debris which leaves land uncultivable. There are additional 2,000 acres in Nanded, Bidar and other neighbouring districts of Maharashtra and Karnataka.”
He adds that using such devices can benefit farmers by increasing their cultivable land, which is already shrinking, and enable them to earn better income.
When asked whether the thought of failing ever occurred to him while building the machine, Deepak says, “It was difficult to take the risk, as getting a job after graduation is important, and the initial years are crucial for career building. But I never thought about failing or ever intended to make a machine for commercial gains. My aim was to help the farming community. Education is valid only when the knowledge is useful for someone in need.”
For now, he is hopeful his product will be market-ready soon and make way for commercial use in farms across India.
Edited by Divya Sethu
No comments:
Post a Comment