Hailing from Annamangalam, a small and quaint interior village in the Perambalur district of Tamil Nadu, A Jegatheesan recalls how the construction of houses in his village has transformed over the years.
The civil engineer notes that the old houses, which were once built using mud, are now being replaced with concrete structures due to the popular belief that concrete is stronger than mud.
This observation didn’t strike him until he was approached by someone in his village to demolish their mud house to build a concrete one. “Though I have been constructing concrete houses, this particular incident made me reflect upon the transformation of the village houses. The village was once full of mud homes. Today, almost 90 per cent of these traditional homes have vanished. That’s why I thought of building a mud house on my own to preserve it as a symbol of our tradition and to prove that they are as strong as a concrete building,” Jegatheesan tells The Better India.
Besides, he wanted a house that was close to nature. “I was determined that I didn’t want to cut a single tree while constructing my house. Also, to make it as sustainable as possible, I focused on reinforcing the concept of reuse by sourcing waste/used wood and metals,” says the 31-year-old who built a 1000 sqft house using unfired mud bricks made of red soil and mortar made of the same by reducing the usage of cement up to 50 per cent.
So in 2021, after finishing a three-month course, Jegatheesan started building his dream home that he now calls ‘Thaimann Veedu (which means mother earth in Tamil)’.
The construction was completed within a year and cost him around Rs 20 lakh.
Embracing tradition
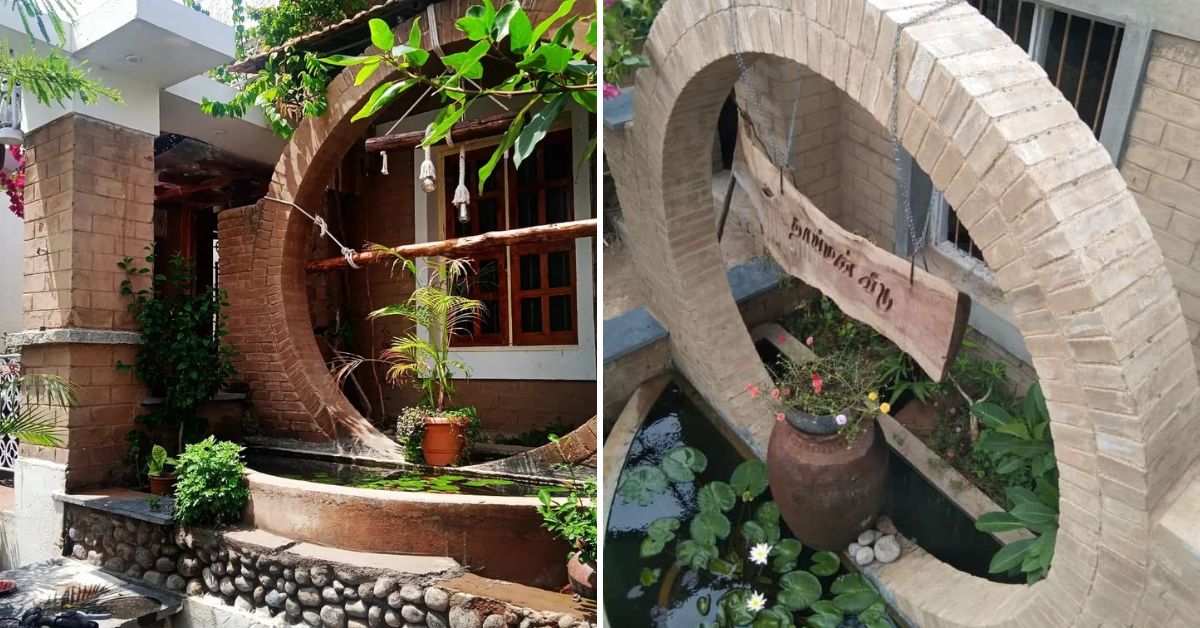
In 2020, while Jegatheesan was still in the planning stage, he recalls that he was a bit unsure about how to go about it as he wanted his house to be as unique as possible. “I wanted to build a multi-storeyed mud house, as single-storeyed ones were common. So, as a first step, I talked to several people who owned mud houses to grasp the pros and cons. After listing them, I realised that there are more pros than cons to mud houses, but people are unaware of it,” he says.
His next move was to learn innovative techniques to build the mud house and therefore he enrolled himself at the Auroville Earth Institute in Puducherry, which promotes and teaches earth-based technologies that are cost and energy efficient. “That’s where I learned about making Compressed Stabilised Earth Blocks (CSEB) or unfired bricks and Arch Vault Dome (AVD). I spent around a year as a volunteer at the institute and learnt that, unlike the normal burnt bricks, these mud bricks are unfired and are made using red soil available in the site, within a 30-metre radius,” he explains.
Jegatheesan says that there is often a misconception that unfired bricks are not long-lasting and they would dissolve when they come in contact with water. “But that is not the case. These bricks are made using a mixture of red soil and a small amount of cement. They are mixed and stamped out mechanically, and then kept for at least three weeks, alternating between sunlight and shade before they are used for construction,” he says, adding that these bricks are strong, efficient, and highly sustainable as they cut the need for burning firewood in kilns.
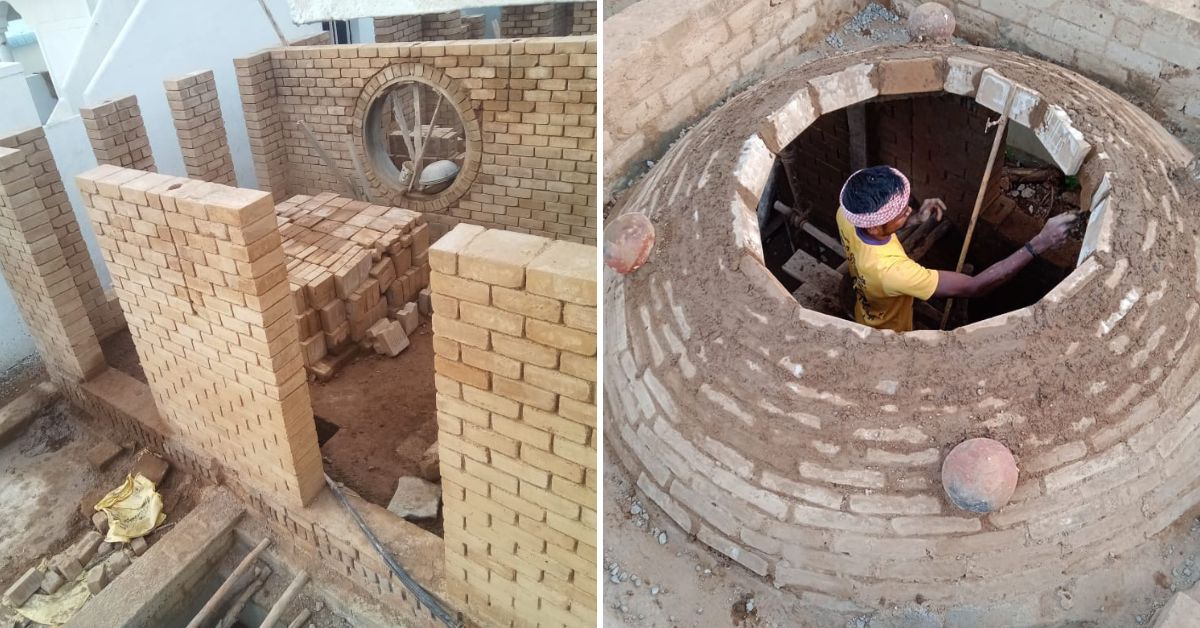
The 1000 sqft house has been built on a stone foundation and adopted the load-bearing technique in which the loads are transferred to the foundation through walls. Besides the unfired mud bricks were laid using a mortar made from the same material instead of using cement in the conventional method.
“The best thing about using unfired mud blocks and mortar is that the walls become breathable. They keep the house cooler in summer and warmer in winter. So, we don’t have ACs at home neither do we need fans most of the time,” says Jegatheesan adding that
Another unique and sustainable technique he adopted was to build vaulted, arched, and dome-shaped roofs. This helped him in reducing the amount of cement and metal used usually in the construction of roofs. “We used around 10,000 unfired bricks instead of cement or metal rods and the roofs are even stronger than a concrete roof,” he explains, adding that the spaces between the domes and arches of the ground floor roofs were filled with debris and were flattened for levelling the first floor.
“We have used oxide flooring throughout the house including the kitchen and bathroom,” he says adding, “We haven’t cement plastered the house except for certain areas like bathroom walls and the kitchen, which are prone to moisture risk. After plastering with cement we topped those areas with oxide. We also painted a light coat of whitewash for the interiors to make them look brighter other than that we have left the walls as it is”
Talking about lighting, Jegatheesan says that he has built his house in such a way that there is natural light inside the house throughout the day. “I also built a courtyard kind of a space which lets in ample sunlight,” he says, adding that with less usage of lights, fans and no ACs they have been able to save a lot in current bills.
“We get around Rs 20 or Rs 30 as electricity bills once in two months. With the Tamil Nadu government’s subsidy, the first 100 units are free and we barely exceed that limit,” he adds.
Repurposing and recycling wood & metal
Another highlight of Jegatheesan’s house is that not a single tree was cut to build the house. Therefore, he sourced old and waste wood from demolished houses and repurposed them for better use. “All the window frames, doors, etc. are all from an old demolished house. I have also used waste wood from different places to build the staircase to the first floor,” he points out.
“I have used chain sprocket of two-wheelers to make the terrace railings, window grills, and a small gate in front of the main door. For that I collected over 1,000 of them from scrap shops and workshops,” he adds.
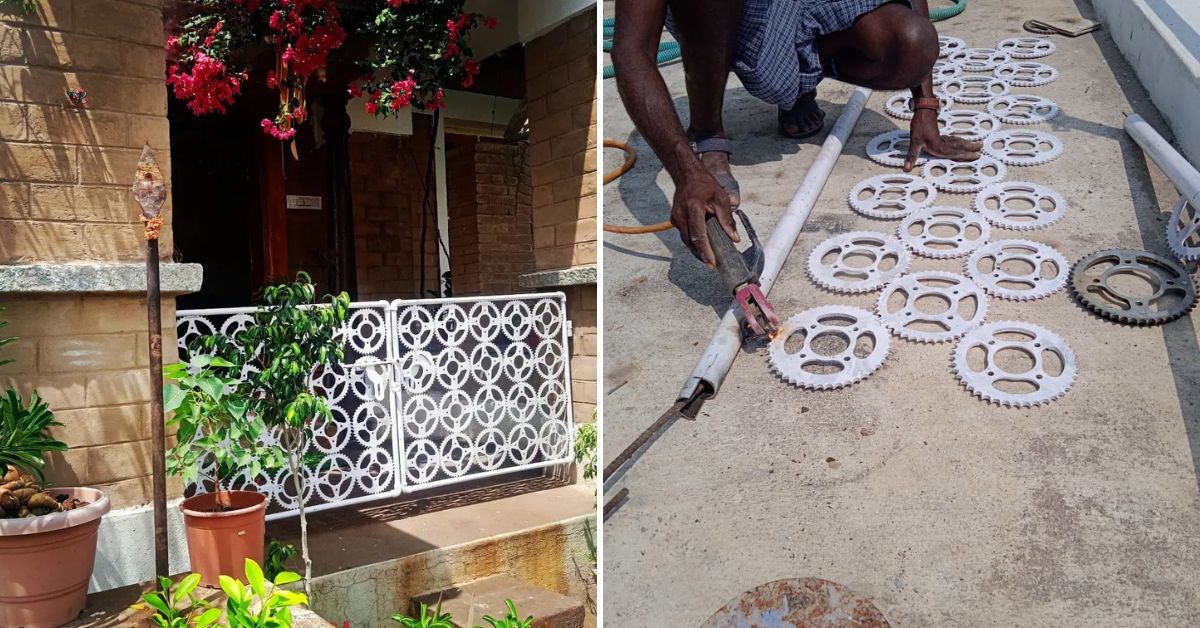
Jegatheesan says it was challenging to train the labourers to work around unconventional methods. “It was labour intensive and hence time-consuming. Another challenge was to convince my family who were doubtful about building a mud house instead of a concrete one.”
The ground floor of the house comprises a porch, a living space, a kitchen, and a bedroom with an attached bathroom. Meanwhile, the first floor has a bedroom, a storage space, and a small room.
“I built a platform through Ferrocement, which is a construction method using wire meshes and cement mortar to place the mattress. It is like an inbuilt furniture replacing the usual wooden bed cot,” he says, adding that his favourite part of the house is the kitchen.

A rainwater harvesting system is also in place with a capacity of 20,000 litres.
Jegatheesan says, “I wouldn’t say that it was a low-budget construction. But I am happy and satisfied that I could fulfil my purpose of building this house — to prove that mud houses are stronger and more sustainable than conventional concrete houses.”
Edited by Yoshita Rao
No comments:
Post a Comment