Rashi Agarwal’s final year of college was incredibly enriching. She embarked on a nationwide journey to explore traditional art and craft forms, all for her thesis. From Delhi to Jaipur, Kutch to Ahmedabad, and Puducherry to Pune, she sought out artisans, absorbing their knowledge and techniques.
Despite the diversity of art forms she encountered, there was a unifying thread among them all — the dwindling demand for handcrafted work as society gravitated toward machine-printed art.
How could this 25-year-old find a way to provide a livelihood to these artisans? This question gnawed at the Surat resident even after she returned home.
It was around this time that she began painting the cover pages of diaries, which were highly appreciated by her friends and family. Since most of the artisans she visited worked in the paper industry, she wondered if she could turn her love for drawing and painting into a business that would provide employment to people who worked by hand.
She wanted to revolutionise the space by making these age-old practices of handmade products appealing to today’s consumers and bringing them back into trend. With this thought in mind, Rashi started ‘Roohani Rang’ — a handmade stationery business that sells sustainable products.
What makes the venture stand apart is that the products — be it diaries, planners, calendars, and more — are made out of cotton waste. So far, Rashi has sold over 15,000 planners and employed over 50 artisans, while recycling 9,732 kg of cotton.
No trees were harmed in making this paper
During her final year of bachelor’s at the Raman Bhakta School of Architecture in Surat, Rashi decided to venture into business. The catch — it was 2020, the second wave of COVID-19 was wreaking havoc across the country, and the then student had just Rs 5,000 to start her business.
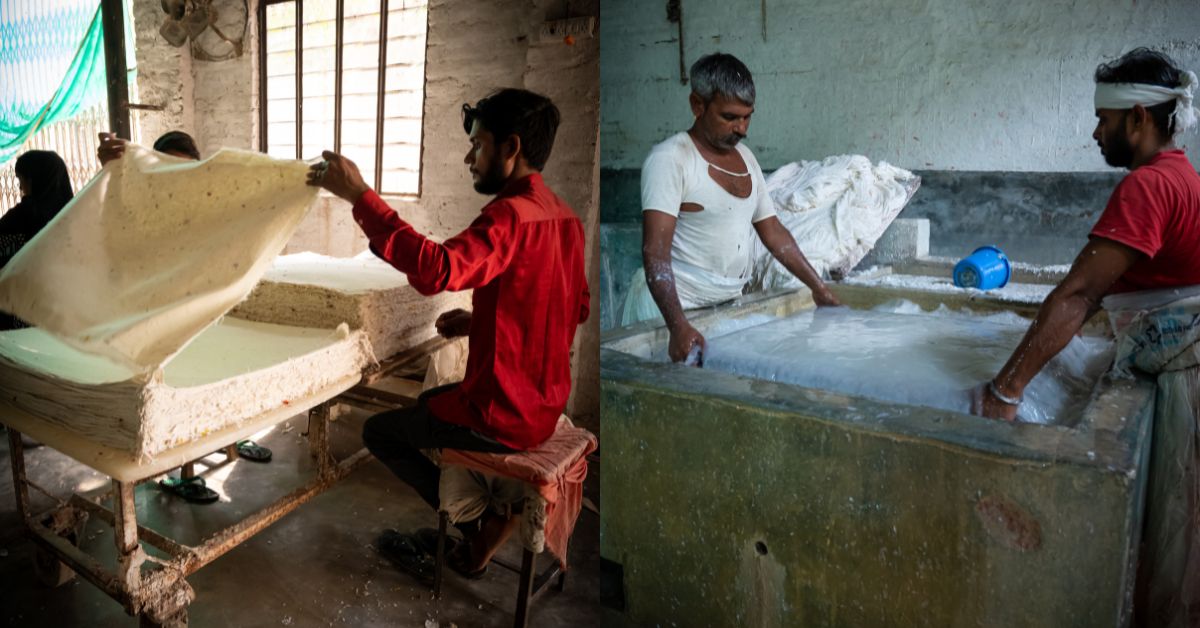
She still decided to take on the challenge head-on, as she remembered the words of the craftsmen and women she met. “Most of them had no work due to COVID-19 and were struggling to make ends meet. They were desperately in need of work. I was acutely aware of their reality as I spent several days with them. I knew that I had to help them,” Rashi tells The Better India.
The architect decided to start in Jaipur and revisited the artisans, explaining her idea to them. After spending a few days with them, she got them on board with her vision. With her initial investment, she produced 50 diaries.
Given the tremendous reception, she reinvested the money to expand her product range to include more stationery items — such as planners, calendars, notebooks, journals, sketchbooks, and more. Her goal was to bring change in the artisanal space by introducing smart design interventions and fostering synergy between designers, artisans, and the end consumer.
Rashi chose to employ paper-making techniques that have been practised in India for centuries, such as handmade paper making, hand stitching of paper, table-top screen printing, and hand block printing. Every product of Roohani Rang is meticulously handmade, devoid of any chemicals or dyes, according to the founder.
“My idea is to use these old techniques and make them relatable in today’s world. As a designer, I want to preserve these crafts by producing them in a way that is palatable,” she adds.
Roohani Rang recycles cotton waste to make their stationery. They use miniature painting, Gond art, Madhubani art, and Tanjore painting in their products.
Recycling cotton waste into bespoke stationery
The production at Roohani Rang is a long-drawn process and starts with procuring pre-consumer textile waste from factories. Pre-consumer waste refers to any excess material that arises during the production of yarn, fabrics and textiles.
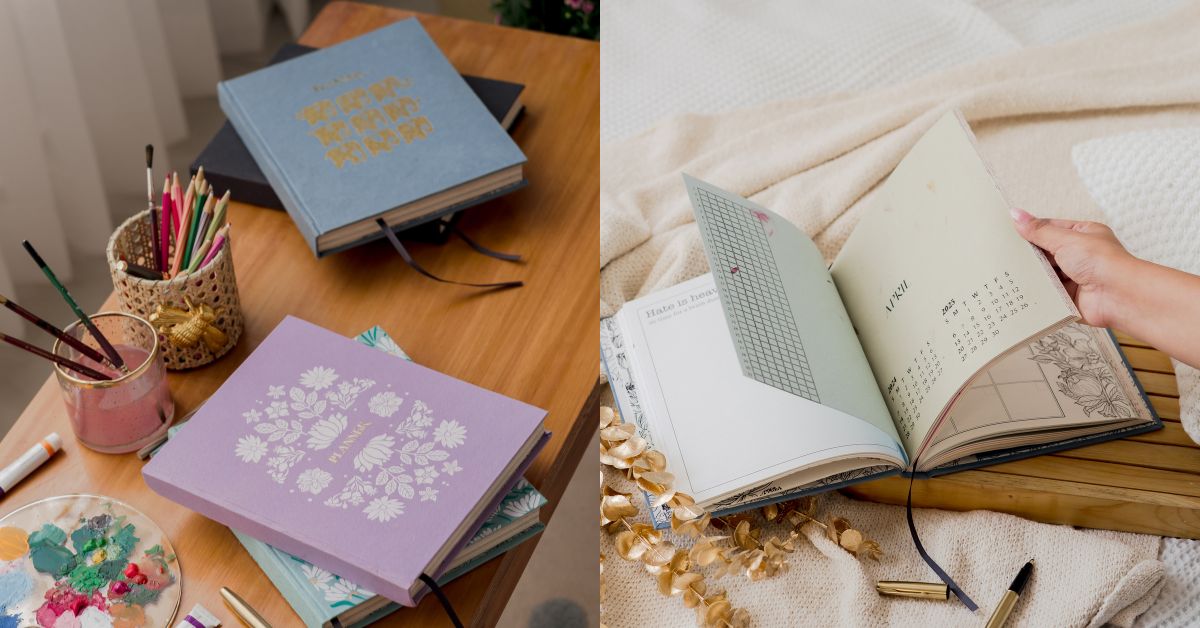
“This waste is usually sent to the landfills and can’t be used to make anything as it’s in small pieces. We decided to use this to make our paper, which is done in many clusters across India, like Jaipur, Ahmedabad and Puducherry. The added advantage of using cotton waste is that it’s already white and doesn’t need any chemicals to clean it up,” adds Rashi.
This cotton waste is then shredded into smaller pieces and converted into paper.
The shredded cotton waste is converted from pulp to paper by the artisans in a pool of water. This water is also reused, mentions Shaunak Desai, architect and partner at Roohani Rang.
The paper is then dried, printed, bound and packed. Every step of the process is handmade, states Shaunak.
Roohani Rang has a warehouse in Surat where they make the prototypes of their products, post which they are produced in large quantities in Jaipur, Puducherry or Ahmedabad. All their products are hand printed and hand bound.
“The paper and printing are done in one cluster, while the binding and packaging are done in Surat. Depending on the kind of product and paper required, we choose the cluster where it would be made. For example, if screen printing is required, we get it done in Jaipur,” explains Rashi.
Shaunak adds that a regular piece of paper requires 10 litres of water to be made, along with the fact that a tree is cut. “Compared to mill-made paper, handmade paper requires 20 times less water. We recycle the same water to make our paper as no chemicals are used. We have made over 15,000 products until now, using over 1,500 reams of recycled paper. Through this, we’ve saved 100 big forest trees from being cut,” explains the architect.
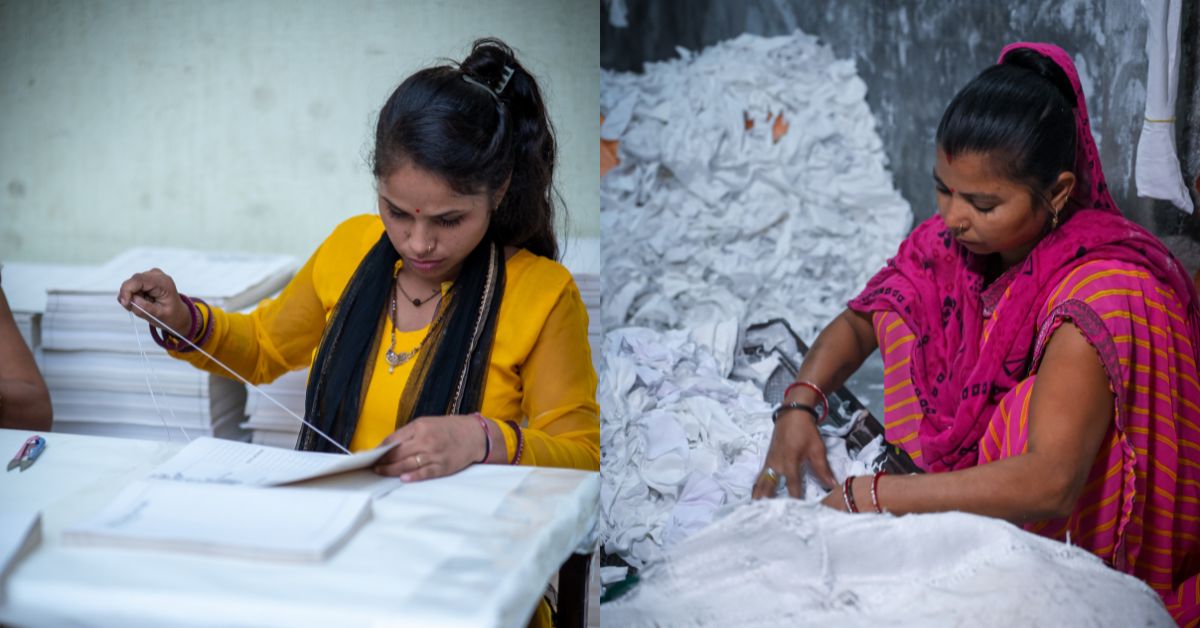
Their products follow a 21-day cycle, as they are made in different facilities and pass through almost 40 hands in the entire process.
Through this, they provide employment to over 50 artisans and have 15 employees. They also promote mental health and share ways to be mindful through their posts on Instagram. In four years, they’ve sold over 15,000 products and have garnered a following of over 40,000 on Instagram.
Rashi wants to expand to ceramics and clothes by 2025. “Why create more waste when we can recycle the existing waste? My mission is to provide a livelihood to artisans who are almost on the verge of extinction, and also to keep their beautiful art forms alive,” says Rashi.
Edited by Pranita Bhat
No comments:
Post a Comment