Every day for the past four years, Mandakini Gogoi and her husband, Rituraj Dewan, have been travelling from their home in Guwahati, Assam, to the forests of the Loharghat range. It is largely a mix of business, pleasure, passion and hard work that encourages their daily grind to certain small villages there. They are very comfortable with the village folk, who come to the centres they have created in the region to spin, weave, dye and churn out miraculous textiles that are created, honed and polished before sending them off to the Indian market and also to many foreign buyers.
The best part? They do it all with the help of their small team—a mix of local artisans and some textile experts—without causing any damage to the forest area where they work. Instead, they help in maintaining the ecological balance of the area. Considering that this area of Assam is one of the most biologically rich and also among the most heavily threatened, for frequent tree felling and poaching incidents, this is no mean feat. There are quite a few NGOs and other companies that work here but not everyone can claim to preserve the biodiversity of the region or even ensure that local artisans get a fair price for their hard and uniquely skilled work.
Slow Fashion Beckons
It had taken Mandakini and Rituraj years of research before launching 7Weaves Social Pvt Ltd, a sustainable textile unit, in June 2017. The name is a tribute to the textiles or weaves from the ‘Seven Sisters’. They looked into the region, its people, possible textiles to be produced, the know-how of the business of sericulture — a common practice in Assam where silkworms are reared to produce cloth, particularly the Eri silk fabric procured from Eri silkworms.
It also meant they needed to study global markets and trends for the demand of this fabric and have it worked upon by the locals of the forest area, who mostly learn to weave and spin as part of their family tradition.
The challenge that faced them was to produce textiles that would make the cut internationally while not harming the environment and ensuring fair wages to the artisans. Both Mandakini and husband Rituraj were formerly employed in the healthcare sector and it was her dream that led to both of them quitting their corporate jobs and returning to their home state to set this up.

“It was a huge task for people like us who had no knowledge of an industry like this, leave alone methods like spinning, weaving and working in close tandem with village people with whom it takes time to build a rapport and earn their trust,” admits Mandakini, who wanted to provide gainful employment to the women.
From stumbling through every step to visiting international fairs and markets, the husband-wife duo’s efforts have now been awarded a Certificate Of Excellence from the Ministry of Textiles, Government of India and the HEPC (Handloom Export Promotion Council).
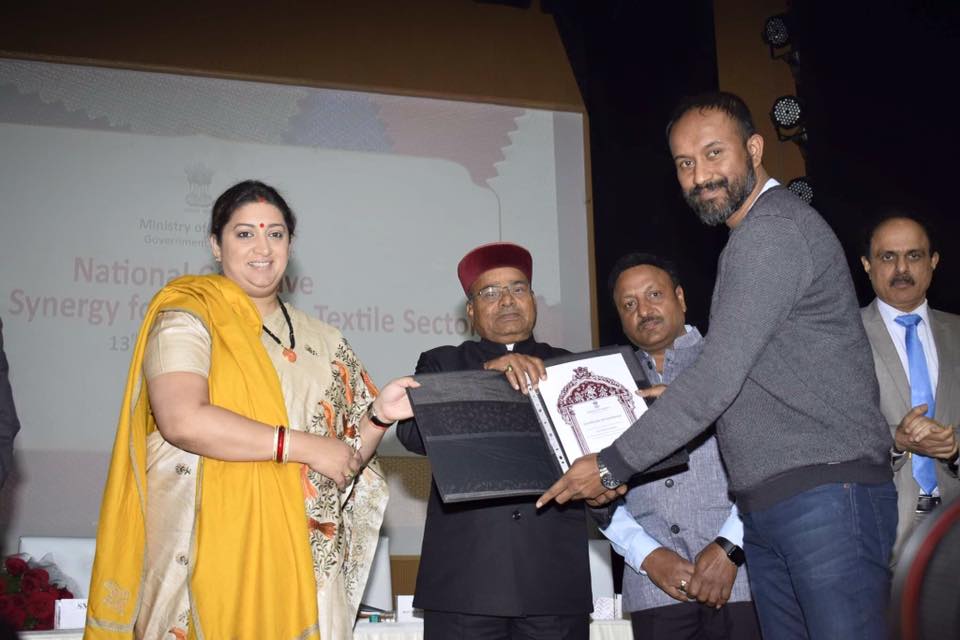
“I have been a proponent of preserving the ecological balance and protecting biodiversity, since the time I was a school student, actively working towards it and presenting papers in journals. It is a cause that I hold above all, in my life. When we got an opportunity to do that, we followed that road in the blink of an eye,” says Rituraj, who is a former international marketing expert. He adds, “It took some time to figure out how the entire chain worked but now we have a fairly good system in place, thanks to all the studying and research we did that was both practical and theoretical.”
The aim and agenda of 7Weaves is a wholehearted focus on ‘slow fashion’, which means producing something mindful, holistic and slow. These products have a slower production schedule, small-batch collections and zero-waste designs that try to reduce textile waste that clog landfills. Therefore their model is mapping the future for sustainable, ethical textiles.

“Eri silk rearing is a traditional practice of the indigenous communities who live in the Indo Burma biodiversity hotspot. The process is based on traditional ecological knowledge of the community who share the biome. The 7Weaves model works with the community to work on a small surplus without changing the current status quo and incentivise the people for sustainable use of resources and long term conservation which leads to biodiversity conservation,” says Mandakini.
The term ‘Womb To Weave’ is applicable here as the silkworms are reared in their company’s centres, and then the process of waiting begins as the worms start making their cocoons for hibernation. It is only when the worm leaves the cocoons, out of its own accord, that the cocoons are gathered and the village women begin the process of sorting the thread. Then the weaving begins.
While they have international experts on their panel to guide them, they also welcome trained people who are passionate about the environment to help them achieve their objective. Textile designer Sneha Chaudhury, a NIFT graduate, who is from Lucknow and has now shifted her work base to Assam says, “It has been a different and very interesting learning experience for me and though initially, it was difficult communicating with the village folk; now, it’s easier. We work in tandem. They weave their designs and I tell them about what will work in terms of trends that will sell internationally.”
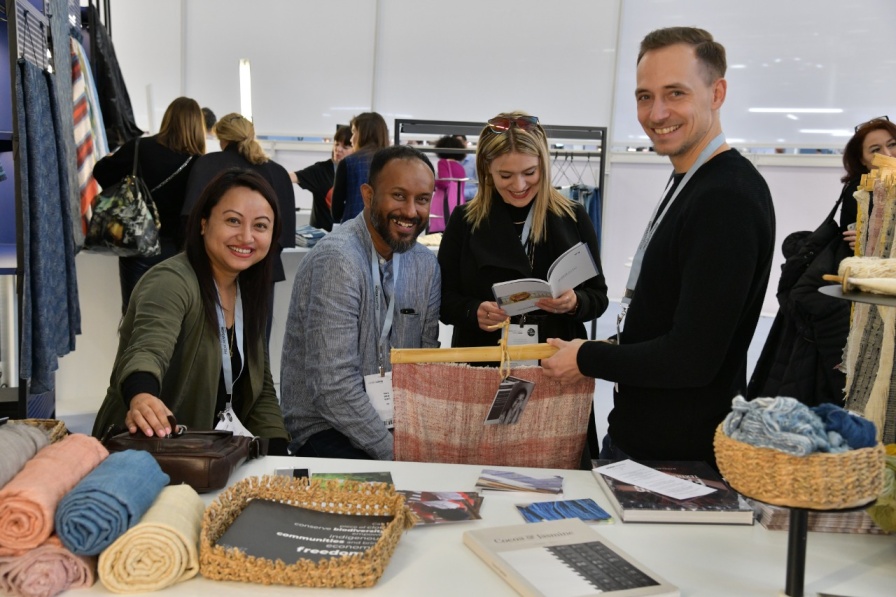
A Sustainable Step Forward
The entrepreneur couple soon realised that to produce textiles from natural sources and protect the environment, one has to work only with indigenous communities. “They belong to the region so we cannot dispute their knowledge and understanding of the region that needs to be preserved and yet it will also provide them with a source of livelihood,” says Rituraj.
The indigenous communities still maintain traditional knowledge regarding weaving with natural fibres and dyeing with natural materials. Local weaver Surabhi Rabha, a soft-spoken 25-year-old who has been with the company since its inception and now trains new weavers and supervises all weaving schedules says, “I used to weave in my home earlier and take a few orders that I would get on and off. After I joined, work has become more regularised and systematic and it is useful for me because this skill that is passed down through the generations will otherwise disappear. I earn about Rs 6,000 monthly. We are also covered under a corporate medical policy of Rs 5,00,000 each and entitled to get 50 per cent of the profits of the company annually.”
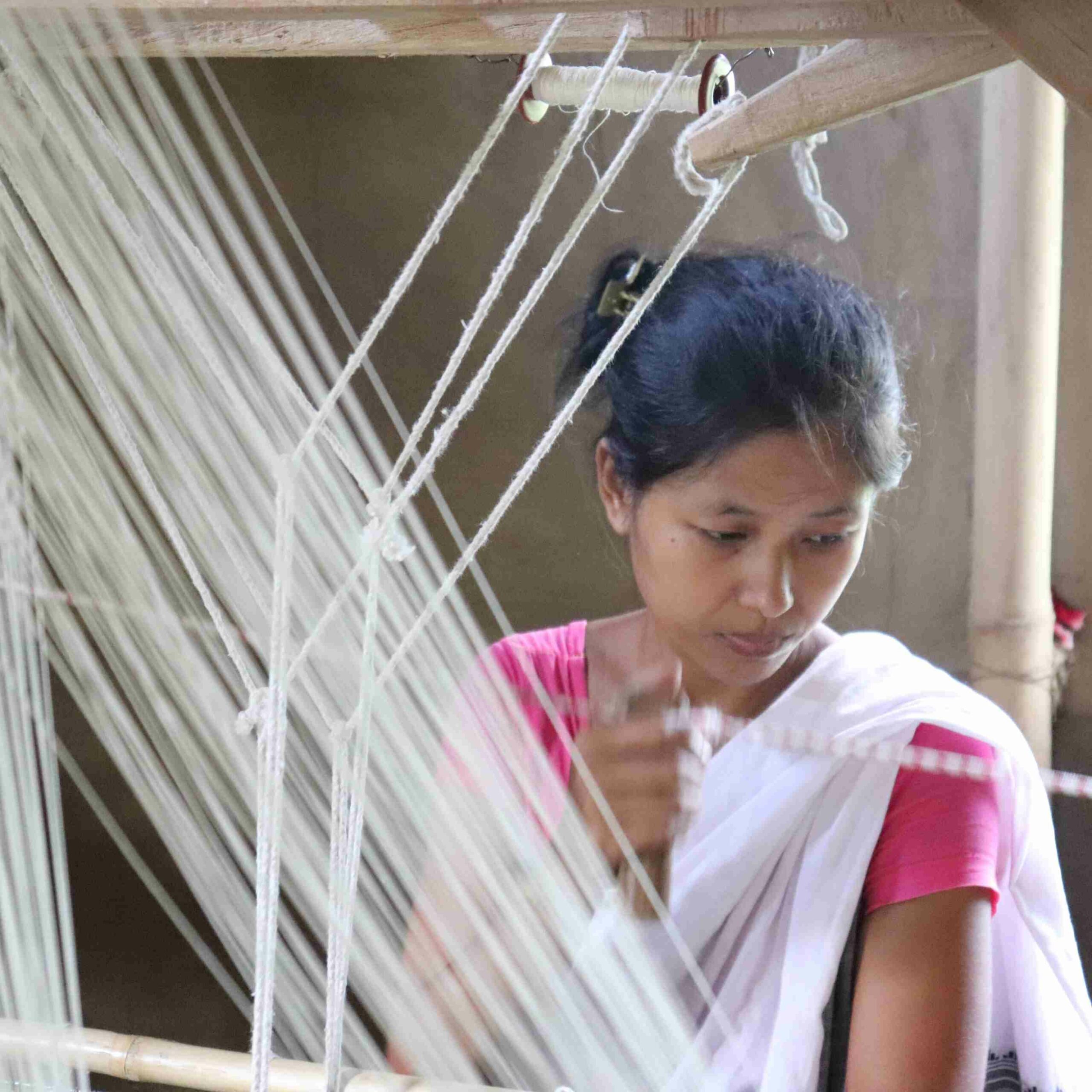
Every piece of cloth produced here helps restore the rich biodiversity of the area. The community reduces waste by only using what is necessary and planting and replanting crops and herbs that can be used for their dyes.
As more and more plants are identified for their economic value and sustainable use, conservation becomes integrated as an important part of the livelihood of the locals. “Our onus is on skilled local people getting their fair dues. So, we usually pay them 50 per cent of the profits annually plus a fixed salaried income, irrespective of the work output. We chose the Eri silk particularly because we felt it has a great future,” explains Mandakini.
Eri silk production is also one of the least harmful methods of sericulture as the worms that produce silk are not killed. Their cocoons are harvested right after the silk worms leave them. Hence Eri silk is also called the ‘Ahimsa’ silk.
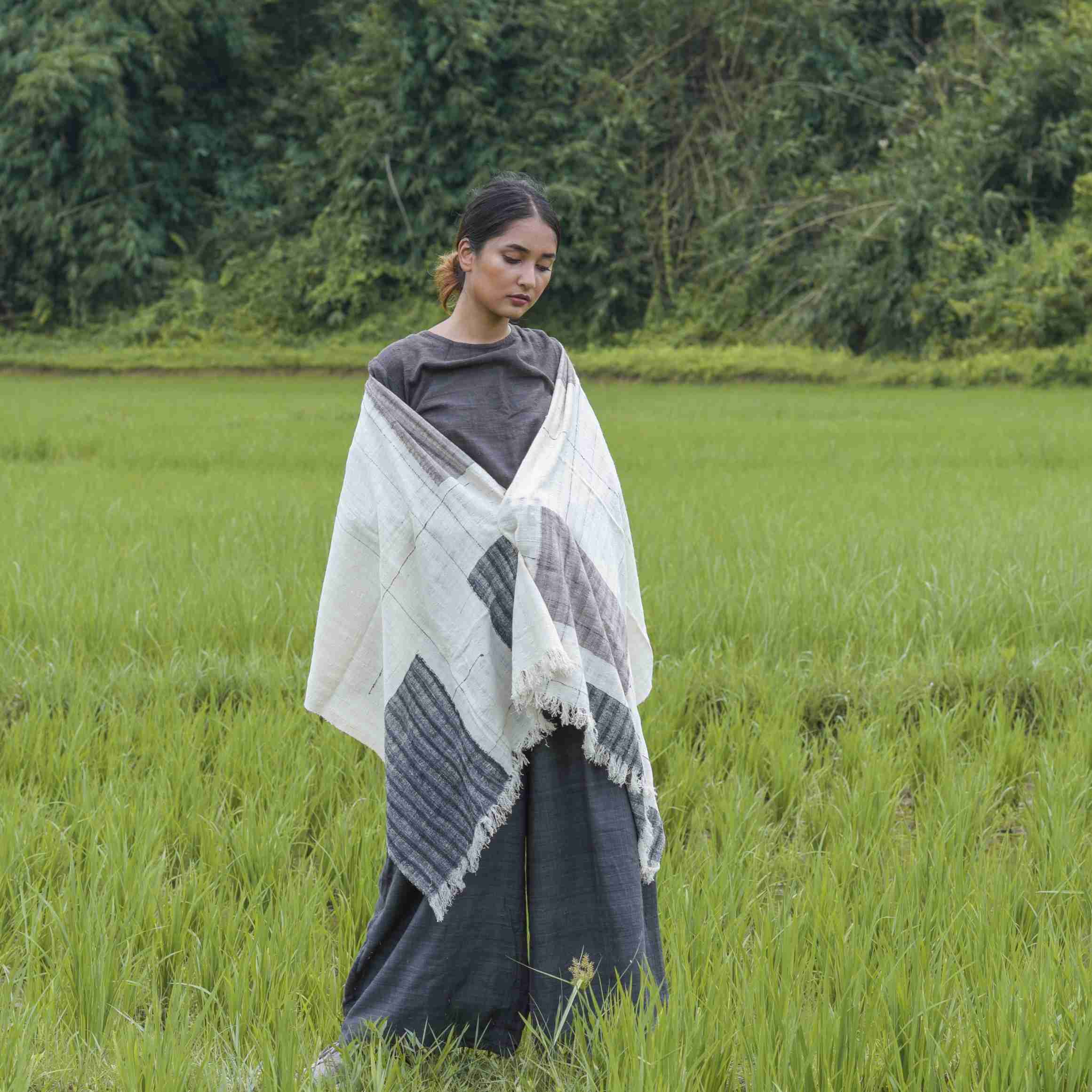
As for the markets, abroad and in India, they are slowly but surely recognising the potential of this unique venture. Their regular buyer, Carolin Hofer of Jyoti Fairworks, who is based in Germany says, “We have been with 7Weaves since their inception and we were impressed by not only their beautiful fabrics but mostly their holistic vision, the people and the eco-friendly nature of the business. They clearly are one of the most inspiring undertakings that we have met along our journey being a fair fashion label and an important ally in the movement towards a more sustainable textile industry.”
She adds, “Eri silk has appealed to us and many of our customers, as it has a great and very original story to tell with amazing thermal characteristics — keeping you cool in summer and warm in winter. I believe in its potential in the textile market, especially with the currently growing awareness for sustainability. We are currently working with companies from France, UK, Belgium, Germany, Australia, Canada and Japan. There are two kinds of orders that we do: sampling and production. Sampling takes about 4 to 6 weeks and production can take up to 6 months. Our production orders range from 450 to 500 metres per month.”
And what does the future hold for 7Weaves? “Opening more centres and diversifying into other textiles, which we are already doing and continuing to provide gainful employment for the upliftment of local artisans, especially with a focus on women’s empowerment,” Mandakini signs off.
(Written by Tashneem Ali Chaudhury; Edited by Yoshita Rao)
No comments:
Post a Comment