Tvasta Manufacturing Solutions, a deep tech startup founded by three alumni of IIT Madras in 2016, has created history by constructing India’s first 3D-printed house. Constructed on campus with a built-up area of about 600 square feet, this single-storey home consists of a single bedroom, hall and a kitchen.
According to the company, “Tvasta’s ‘Concrete 3D Printing’ is an automated manufacturing method for constructing three-dimensional real-life structures (at all realisable scales). The technique utilises a concrete 3D Printer which accepts a computerised three-dimensional design file from the user and fabricates a 3D structure in a layer-by-layer manner by extruding a specialised type of concrete specifically designed for the purpose.”
Developed in collaboration with Habitat for Humanity’s Terwilliger Center for Innovation in Shelter, the ‘Concrete 3D Printing’ technology employed has multiple advantages:
-Potentially reduces overall construction cost significantly
-Order of magnitude difference in overall construction time
-Brings down the related carbon footprint
-Increases productivity of labour involved
-Offers raw material flexibility/utilisation of eco-friendly materials.
Speaking to The Better India, Adithya VS, the CEO of Tvasta Manufacturing Solutions, gets into the details about their indigenously developed technology.
“Tvasta’s 3D Printing technology is built to bring digital technological advantages to the realm of construction. The focus is to make the process available to all sections of the construction industry, including affordable housing and large-scale infrastructure building. The reduction in overall time required for construction involves an order of magnitude change. What would require months to build can be built in days. Currently, the capability is to print the superstructure of a house that would require 4 to 5 months to build conventionally in about 5 days. The technology has also been designed in such a way that it is sustainable and green. The material used contains industrial waste and recycled material. This reduces the overall carbon footprint of the structure during construction,” notes Adithya.
But the technology goes beyond that. The houses built using 3D Printing are customised for geographical and climatic conditions that exist in an area. As a result, any additional heating or cooling requirements—mostly cooling in India—are very minimal for the structure. This will ensure that the energy consumption of any structure that is built will be very minimal, claims Adithya.
“We’re currently studying the carbon footprint that the structure reduces over its lifetime along with IIT Madras. Also, the construction cost of a house or any large-scale structure depends on several factors. It depends on the design of the structure, the city or geography in which it is being built, soil properties, number of structures in a specific project, etc. Considering the nature of the current projects, we are estimating 20-30% savings compared to conventional construction in our projects. We are working with several institutions to make this technology even more affordable in the construction domain,” he says.
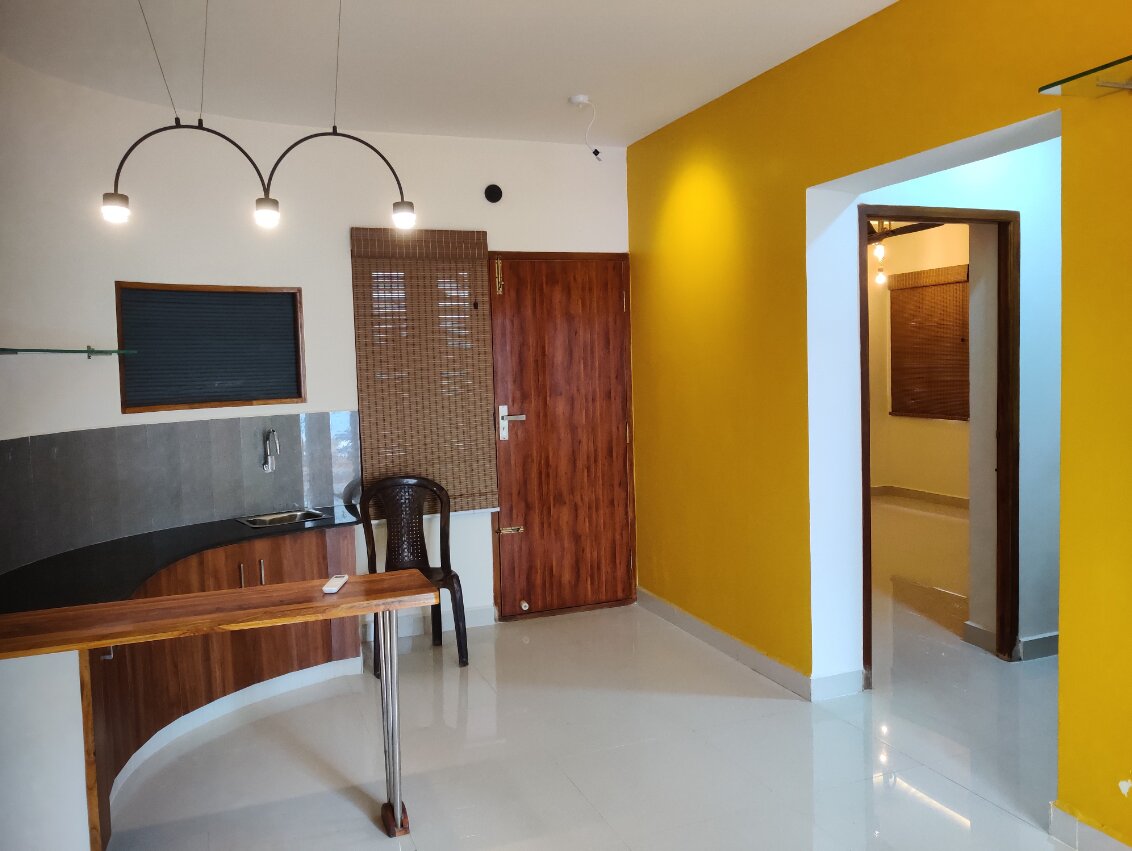
How does 3D Printing reduce construction cost and save time?
Adithya explains, “The cost reduction is achieved by increasing the productivity of workers who are involved in the construction process. A structure that would take months to build can be done in a matter of a few days; this contributes to tremendous savings on the time and cost of capital. There is also a saving on the amount of material used as 3D Printing reduces wastage and the total amount of material required to build a structure. The saving on time is primarily brought in by the employment of robotics and automation technologies.”
He adds, “Construction is one industry where precision automation has still not taken root, unlike the automotive industry. Through the actions of a 3D Printer that can receive instructions to build a large-scale structure in the form of a 3D Virtual file, a large-scale structure can be built without formwork or molds in a very short period through layer by layer manufacturing.”
This structure was built to show the research, development, and manufacturing capabilities that exist in India, although there are plans to use it as a conference centre at IIT Madras.
It took about 21 days to 3D print this particular structure due to COVID-related restrictions. Currently, the company has the capability to 3D print such a structure in about five days.
“The company is currently working on scaling up this technology to make it available throughout India. For this, the company has partnered with several large-scale construction companies and institutions. The Ministry of Housing and Urban Affairs has also given wings to the project by providing support through the ASHA Incubator programme under the Global Housing Technology Challenge launched by the Prime Minister,” says Adithya.
The material used for construction is a proprietary 3D Printable Mix developed by the company. Having said that, materials such as mud and other natural solutions can be used for construction. Adithya goes on to claim that the company has plans to introduce such green materials into the construction space in the future.
Lauding the work done by the Tvasta, Prof Bhaskar Ramamurthi, Director, IIT Madras, says, “This technology is the first to be beneficiary-led in the construction industry. The machine for constructing this house can be rented, like borewells rented by farmers. It provides for large-scale, high-quality and also, price assurance for the customers.”
Meanwhile, Union Finance Minister Nirmala Sitharaman told media persons attending the launch of this home, “India definitely needs such solutions which do not require much time. This technology enables building a 3D-printed house in 5 days. With the Prime Minister’s goal of ‘Housing for All by 2022,’ we have a huge challenge before us. A huge challenge of meeting that deadline and making sure that people who need houses get it at an affordable price. Conventional housing requires timing, material, logistics, transporting of material, and so on. But if this technology can produce houses in different locales at five days per house, it would not be a big challenge to build 100 million houses by 2022.”
(Edited by Yoshita Rao)
No comments:
Post a Comment